ABOUT AERZEN USA
Aerzen USA was founded in the United States in 1983, and is a wholly owned division of the German manufacturer, Aerzener Maschinenfabrik GmbH. Founded in 1864, Aerzener Maschinenfabrik is a recognized world leader in the production of rotary positive displacement machines since 1868.
Continuous improvements in our production facilities, staff training, and innovations in our product offerings provide our customers with the best product and service available in the blower and compressor market today.
Our presence in North America has grown steadily since our establishment in 1983. Our customers are most pleased by the dependable operation of Aerzen blowers and compressors, low life cycle costs, and Aerzen Quality as a standard.
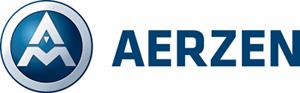
CONTACT INFORMATION
Aerzen USA
108 Independence Way
Coatesville, PA 19320
UNITED STATES
Phone: 610-380-0244
Contact: Chris Cherubin
FEATURED ARTICLES
-
AERZEN, a leading global provider of reliable, high-performance, and energy-efficient blowers and screw compressors, is excited to announce the appointment of John Ansbro as President of Aerzen USA Corp. With over 30 years of experience in the industrial sector, Mr. Ansbro has a strong history of driving growth, operational excellence, and cultivating customer-focused cultures.
-
It is all too common for bakeries to end up with blowers for their pneumatic lines that are not the right size. Explore how to avoid long-term problems and costs associated with an under-sized system.
-
A new study shows Tyson Foods, the second-largest meat processing company in the U.S., dumped more than 371 million pounds of pollutants into U.S. waterways during a five-year period between 2018 and 2022.
-
AERZEN, a global company delivering reliable, high-performing, and energy-efficient blowers and screw compressors, is pleased to announce the appointment of Kristen Grunza as the President of Aerzen USA Corp.
-
Conveying food products over long distances requires careful consideration of multiple factors, including material, temperature, pipe diameter, and blower motor size.
-
Energy efficiency should never come at the expense of capability in a pneumatic conveying system. Here’s what you need to consider in order to balance them both.
-
On January 19, 2022, Aerzen USA announced the acquisition of Vooner FloGard® Corporation, headquartered in Charlotte, North Carolina, with manufacturing operations in Greeneville, TN. Vooner is a premier manufacturer of vacuum pumps and vacuum system components.
-
As the wastewater industry dissects the $1.75 trillion federal Infrastructure Investment and Jobs Act to understand how much will flow to us, it’s important to note that wastewater treatment projects at the local level continue to pass city approvals and find funding.
-
A confectionary was experiencing condensation issues getting large batches of sugar into their production plant. See how Aerzen provided a significantly improved, stable solution for unloading sugar.
-
Bulk delivery of basic food ingredients — such as sugar, flour, soy, and food powders — presents inherent issues at the point of unloading. Discover a safer, more efficient alternative for faster unloading.
-
There are many instances in which food and beverage plants may need a temporary solution to a system or process that requires low-pressure air – the largest of which are within onsite wastewater treatment plants.
-
Installing the most appropriate blower equipment in the process can enhance yeast and enzyme production, minimize energy costs, guarantee food safety, and avoid costly failures.
-
In addition to penalties for non-compliance, wastewater treatment plant (WWTP) operators in the food and beverage industry risk excessive losses caused by problems at the wastewater treatment facility.
-
A grain mill needed a way to extend its conveying height from 45 to 65 meters, putting added strain on its compressed air systems. Keep reading to learn how a hybrid solution helped the mill meet its goals.
-
The economical operation of a wastewater treatment plant depends largely on the design and the interplay of the aeration and process controls. Moreover, the human factor and the management objectives are at the heart of the plant’s reality and should also be taken into consideration. Selection and thoughtful integration of all the subsystems is of paramount importance.
-
By following basic best practices and working with a trusted partner, food processing companies can make incremental increases to their production capacity without disruption or excess cost.
-
A microbrewer’s expertise is in brewing, not engineering. Discover how you can get the most out of production lines without the costs associated with hiring outside engineers or experts.