4 Ways To Boost Stretch Wrapping Efficiency
By Isaac Fletcher, contributing writer, Food Online
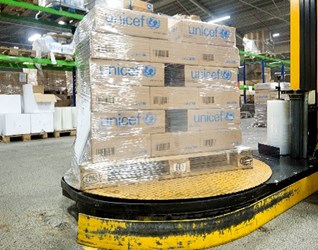
When implementing or upgrading stretch wrap equipment, there are many areas where increased efficiency and cost savings can be found. Some quick considerations can help ensure you make the best investment for your packaging operation
Making decisions regarding what pieces of equipment to implement into your packaging operation can be an overwhelming experience. With the potential benefits provided by efficient and effective equipment, making the right choice can have a significant impact on your productivity. With this in mind, choosing a high-quality stretch wrapper can provide tremendous economic benefits to loading dock operations.
As with many equipment implementations, automation is a great way to provide a cost-effective boost to efficiency. For example, putting in place a system that allows an operator to remotely start the machine means he is free to work on another task while the machine automatically cuts the film at the end of the cycle and attaches it to another load at the start of the next.
Additionally, by making use of a load-to-pallet bonding device — such as affixing loads to a pallet with a cable of film — you can limit the instances of goods being damaged as the result of sliding off their pallets. Savings can also be found by using stretch wrapper turntables that are equipped with built-in scales. Knowing the exact weight of your loads can help avoid paying less-than-truckload (LTL) re-weight fees.
To add further efficiency to the operation, consider implementing a conveyor system that will help reduce the occurrence of bottlenecks in the production line. This can be particularly beneficial if loads are wrapped continuously, as once a load is wrapped; it can be moved to an exit conveyor. This simple equipment addition eliminates the need for an operator to remove a wrapped load from the conveyor before lifting a new load into place.
Lastly, making use of a pre-stretch film delivery system has the potential to reduce film costs by 50 percent or more by elongating the film to enhance its yield. Within this kind of system, two rollers in the film delivery system turn at different speeds, causing the film to stretch. By getting more mileage out of your wrapping, you can greatly reduce material input costs.
As with many production line changes, putting these changes into place comes with some extra costs. However, over the long run, many efficiency-boosting features will pay for themselves, often in just a couple of years.