10 Considerations For Choosing An Automated Line Changeover System
By Isaac Fletcher, contributing writer, Food Online
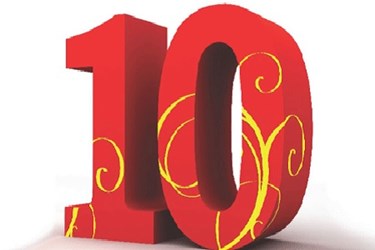
To maximize the potential of an automated, packaging-line changeover system, there are many factors to consider that will simplify the implementation process and provide lasting benefits to your operation
Automating packaging line changeover can provide a variety of benefits ranging from improved production capacity, reduced downtime, decreases in operating cost, more efficient use of workforce, and increased levels of food and worker safety. However, to reap the maximum benefit for your unique operation, it is important to make some critical considerations. With numerous options available to manufacturers looking to implement automation of line changeover, using the following guidelines will ease the process and help ensure the optimal system is chosen.
1. Is operation of the system easy and intuitive? The more steps required for the operator to go through, the higher the risk for errors and the less efficient use of labor hours. Asking questions such as whether or not the operator needs to physically go to every section of the system to complete a given task will help reduce errors and ease system implementation.
2. Does the system require specific operator knowledge related to programmable logic controllers or programming? Some systems provide intuitive user interfaces to simplify use, while others may require more-advanced skills. The easier it is to program new system configurations, the fewer margins for error and possible need for recalibration.
3. How many change points need to be configured in the line and how many are able to be configured with one configuration method? When making this consideration, be sure to account for both current and future needs.
4. Does line equipment changeover need to occur in unison or in sequence? Systems that can be configured in sequence allow for sections to be used for production while others are being calibrated for new settings.
5. Does the manufacturer have the ability to restrict access to certain parts of system operation? The ability to apply varying levels of user access can help protect programmed system configurations while still providing operators enough access to perform their job.
6. How can manufacturer and operator knowledge be leveraged to account for external factors, such as seasonal temperature fluctuations? Systems that afford this kind of flexibility provide manufacturers some of the benefits of manual changeover — such as fine-tuning for details that may not be easily gauged by equipment — in an automated format.
7. Is mechanical backlash something that needs to be accounted for in your line changeover? Make sure that if this is a consideration within a current, manual setup, that an automated system can properly handle the line changeover.
8. If mechanical issues occur within the system, how easily can drives and motors be replaced and reconfigured? For systems where there is little or no need for specialized skills, operating costs can be greatly reduced.
9. What are the technical support options for the system? How easy is it to troubleshoot problems as they arise? Long delays in getting technical issues resolved can slow productivity and possibly result in wasted materials and product. It is also important to choose a system that provides functionality for backing up system configurations in the event of data loss.
10. Can the system be maintained with in-house expertise? If there is a need to depend on an outside party for system maintenance, there can be additional costs and other issues that can arise when dealing with an outside source.