PMMI Study Clarifies FSMA's Impact On Food Industry
By Laurel Maloy, contributing writer, Food Online
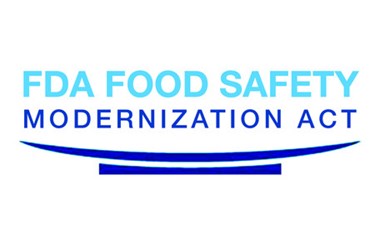
A new report sheds light on the impact FSMA implementation is having on food manufacturing and what rules will most likely require additional investment in terms of time and money
A recent survey, the result of interviews with 64 food manufacturing professionals, gives an up close and personal insight into food manufacturers’ perceptions of FSMA. The Association for Packaging and Processing Technologies (PMMI), in seeking to understand the impact FSMA will have on the industry and how best to help food processors, went to the source. The results of the study more clearly define the role equipment manufacturers must play in the wake of FSMA’s enactment.
According to Paula Feldman, Director, Business Intelligence at PMMI, the study was designed to shed light on the industry’s concerns and to “advise manufacturers on ways to ensure compliance.” A huge source of anxiety for food and beverage processors, the FDA’s ever-changing deadlines have unintentionally heightened the stress associated with FSMA. The FDA, in its effort to be thorough and to have a public conversation regarding the new rules, has inadvertently sent the blood pressure of manufacturing executives soaring.
Relax! First of all, food processing companies will have a period of time to put the new standards into place. Depending upon the size of the company, FSMA allows from one to four years for food processors to comply fully, with the smallest businesses having the longest period of time to adapt.
The study found there are three aspects of FSMA that are expected to have the highest impact on food producers and equipment manufacturers:
- Preventive Control
- Recordkeeping & Traceability
- Sanitary Equipment Design
Of these, food safety experts expect the preventive controls rules to present the most significant challenge. The industry has been in the habit of putting out fires as they occur, not preventing them. Under the preventive controls rules, each facility will be required to have a written food safety plan, clearly outlining the means by which it will prevent or minimize food safety hazards. Additionally, Hazards Analysis & Critical Control Points (HACCP) will play a much larger part. This involves identifying each step of the process where the tiniest possibility exists for contamination; this includes looking at every joint and bolt on the processing equipment. Some processors will choose to upgrade manufacturing equipment, while others will attempt to retrofit existing equipment. Now is the time for food processors to be exploring options and for equipment manufacturers to invent innovative solutions.
Tips For Complying With New Food Safety Regulations
According to PMMI’s study, traceability and recordkeeping are expected to be the most costly in terms of FSMA compliance. That may be true on paper, but when figuring in the benefits for public health and safety, company liability is greatly reduced.
The challenges presented by FSMA’s implementation may seem insurmountable, but they are not. PMMI is just one resource available for the food manufacturing industry. For example, all of the various industry professionals may find inspiration and solutions at PACK EXPO International. Another option is to network with those individuals or organizations being faced with the same issues. An event just held and sponsored by the Institute of Food Technologists (IFT) has a resource library for the IFT Annual Meeting & Food Expo. An Internet search for food processing software traceability provides pages upon pages of solutions. All will be competing for new business as FSMA is wholly implemented in the next few years. This is a good thing!