Packaged Food Manufacturers Guide To Reducing Total Delivered Cost
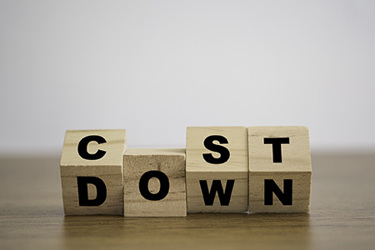
With profit margins being squeezed for packaged food manufacturers, operations managers need to make a robust business case to secure additional capital expenditure. Traditionally, manufacturers have considered Total Cost of Ownership (TCO) in their procurement analysis when purchasing equipment. However, a stronger financial calculation is to quantify how new technology such as product inspection equipment can contribute to reducing the Total Delivered Cost (TDC) of packaged food.
Total Cost of Ownership versus Total Delivered Cost
TCO is made up of all costs directly relating to the piece of equipment, such as the capital expenditure of the product inspection device plus the ongoing maintenance and running expenses. TDC, meanwhile, is the sum of TCO and all operational costs including the physical product, packaging, labor for production and quality checks, waste product, waste packaging and transport.
This eGuide uses the example of a US-based snack food manufacturer to illustrate how technological advancements in product inspection equipment – notably metal detection and x-ray inspection - can reduce the TDC.
Get unlimited access to:
Enter your credentials below to log in. Not yet a member of Food Online? Subscribe today.