A New Level Of Communication Between Food-Processing Equipment And Plant Managers
By Isaac Fletcher, contributing writer, Food Online
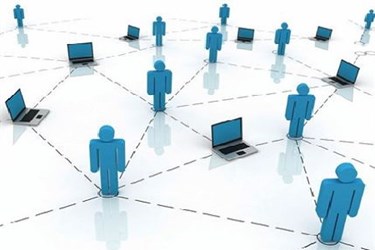
Thanks to the proliferation of new technology, pieces of equipment within a food-production line will soon be able to tell managers exactly what the machine needs to stay running in optimal condition.
Performing regular maintenance on plant equipment is an important part of keeping production lines running efficiently and in top condition. However, it can sometimes be challenging to know when equipment needs to be serviced and what needs to be done. Certain problems may go undetected if routine maintenance fails to evaluate all parts of the piece of equipment. A new innovation may change all that, as food-processing equipment that can communicate to plant managers the exact maintenance it needs will soon exist.
Related: Video — Food-Processing Equipment Is Becoming Faster, Better, And Smarter
Although smart devices making use of an Ethernet connection already exist and have an established position within production lines, these devices have their flaws. For example, they are capable of feeding information to managers, but then that data needs to be analyzed in order to be at all useful. While it is still a great step in productivity to be able to gather and make use of this information in order to gauge factors such as labor costs and productivity, the need for additional analysis somewhat prevents this information from being used to its full potential.
With advances in technology, Ethernet-enabled machines will be able to provide plant managers with specific instructions regarding what needs to be done to keep the piece of equipment running optimally. For instance, a device that needs cleaning will simply send an electronic message to the plant managers stating that it is dirty and needs to be cleaned. This technological step will eliminate the need for diagnosis and data interpretation, leading to faster responses to specific issues and the minimization operational inefficiency.
Related: The Future Role Of Ethernet & The Trend To Decentralized Control Solutions
Additionally, with the world of connectivity and ease of electronic communication, manufacturing execution systems can alert personnel of key issues via mobile alert or text, allowing plant managers to get critical information no matter where they may be.
Unfortunately, the ease of online data exchange comes with some drawbacks. One such concern is the fact that with so much electronic communication, factories may become vulnerable to cyber-attacks. An important element of making sure factories are secure is providing plant staff with proper training for working in an environment with such high levels of connectivity. Just like other safety issues that can arise during production operation, cyber security can be enhanced with strict and proper protocols and implementation of best practices.