Coperion
Sales
7901 NW 107th TerraceKansas City, MO 64153 US
800-821-2476
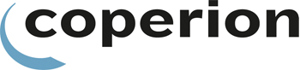
Company Overview
For more than four decades, Coperion screw feeders, vibratory feeders, weighbelt feeders, and bulk bag discharging systems have been the products of choice for pharmaceutical and nutraceutical processes worldwide.