Kaeser Compressors, Inc.
PO Box 946
Fredericksburg, VA 22404 US
800-981-6888
Fredericksburg, VA 22404 US
800-981-6888
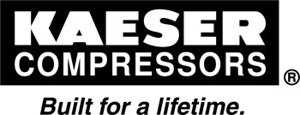
Company Overview
With a heritage that extends back to 1919, Kaeser Compressors is an industry leader in industrial compressed air equipment, including rotary lobe and rotary screw blower packages, rotary screw compressors, vacuum pumps, portable diesel screw compressors, air treatment components and other system accessories. Wastewater treatment plants across the country rely on us for air system solutions that are engineered for long life and continuous energy savings. Our products represent continuing advances in innovation, technology and performance. Kaeser’s built for a lifetime™ quality coupled with our commitment to energy efficiency provide our customers with the lowest life-cycle costs possible.