What's New In Food-Grade Lubricants?
By Isaac Fletcher, contributing writer, Food Online
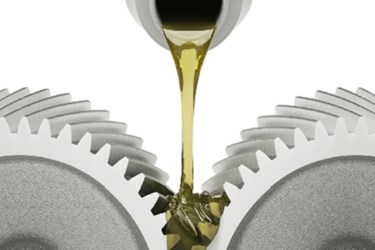
As food processors continuously work toward achieving higher levels of efficiency, safety, and cost-saving, there is a strong demand for high performance food-grade lubricants. Meanwhile, lubricant manufacturers are exploring new ways to meet evolving needs.
In order for food machinery to run smoothly and at optimum efficiency, it needs to be properly treated with lubricating oils and greases. Since there is always a risk of lubricants coming into contact with raw materials, lubricants used throughout the food industry are subject to strict requirements, protocols, and performance and safety expectations. The U.S. Department of Agriculture (USDA) sets the standards and created the original food-grade lubricant designations H1, H2, and H3.
Podcast: The Benefits Of Food-Grade Lubricants
H1 lubricants are those that are used in food-processing environments where the possibility of incidental contact with food products exists. H2 lubricants are used on equipment and machinery where there is no possibility of contact with food. Lastly, H3 lubricants — which are often edible oils — are generally used to prevent rust from forming on various pieces of equipment, such as hooks and trolleys.
Due to the demand for high-performance, food-grade lubricants, lubricant manufacturers are continuously trying to improve products and engineer better solutions to be used in food-processing environments. One such improvement is a new oil specifically designed for overhead conveyors used in the meat industry. The oil is composed of an adhesive synthetic oil, combined with other fluids, which allows the oil to penetrate machinery chains without dripping off.
For many operations in food processing, chains are an essential part of productions. Just like other machinery components, such as gearboxes and bearings, they need to be able to endure the harsh conditions created during food processing. Machinery is often subjected to extreme temperature, moisture, and other strenuous conditions. Accordingly, lubricants used on these pieces of machinery need to be able to withstand the same processing environment.
Lubricant manufacturers are also working with high-viscosity, synthetic-base oils to protect machinery, particularly bearings, under very-high load conditions. Although the base oil is highly viscous, the consistency of the lubricant can be adjusted according to the needs of the application. To ensure that food-grade lubricants are ready to adapt to the emerging trends in food-processing equipment, many lubricant manufacturers are working alongside equipment manufacturers.
Additionally, ExxonMobil has teamed up with an energy consulting firm to help food processors improve energy efficiency by implementing better-performing food-grade lubricants into operations. By using the correct lubricant for a given application, food processors can reduce energy use by nearly 4 percent. ExxonMobil’s efforts are aimed at helping processors achieve ISO 50001 energy management certification. ISO 50001 certification is a set of standards designed to encourage companies to improve their energy efficiency policies, target-setting, and decision making.