10 Ways Checkweighers Can Help Save Your Bottom Line
By Melissa Lind, contributing writer
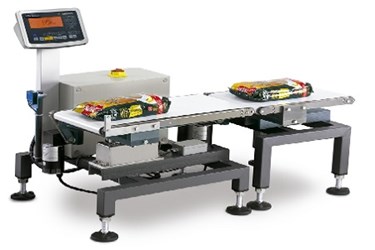
Consistency in the quality of your company’s products helps keep customers coming back. Out-of-specification packages not only present a legal problem, but they can cost your company money as well.
A checkweigher assesses the weight of a product to ensure each finished package's actual weight is uniform with the weight printed on its label. Making sure each of your packaged products meet labeling standards is essential in terms of legal requirements, maintaining customer loyalty, and boosting you company’s bottom line. Here are 10 ways that checkweighing can save your company money:
- Meeting your products’ requirements — your company’s products need to be consistent to maintain consumer loyalty. Checkweighing compares product weight to data limits within your defined limits so that every package is uniform.
- Preventing underweight packages from reaching the market — the United States Department of Agriculture Food Safety and Inspection Service (FSIS) has labeling policies for product weight. If your company is inadvertently shorting customers their product, legal action and customer loyalty challenges could be in your company’s future. Checkweighers help thwart those challenges.
- Preventing overweight packages from reaching the market — though consumers would like to get more product than indicated on the label for the same price, product labeling and product weight have to be accurate and uniform. Overfilling is essentially giving your company’s product away.
- Identifying contamination — in some cases, contamination with certain materials may be identified by weight alone. However, some checkweighers can also be integrated with other product inspection systems, such as X-Ray or metal detection, preventing a costly recall.
- Classifying products — checkweighers can be used to separate and classify products into weight categories and material grades. This saves time on manual separation.
- Accounting for products with missing components — in multi-component products, such as trayed, frozen foods, a checkweigher can identify missing food items simply by checking the packaging’s weight.
- Eliminating imperfect products — checkweighing can help to identify products which have been damaged, are leaking, or are otherwise unacceptable for shipping.
- Ensuring secondary components are included — the product may have been verified as complete, whole, and undamaged, but secondary components, such as spoons or package inserts, may be missing. Checkweighing can help your company avoid this situation.
- Creating a control loop for efficiency — data coming from the checkweigher can be automatically looped back to your filling station. This can help increase efficiency in the production line.
- Preventing nonconformity of lots — as part of your company’s quality control process, deviation data can be easily collected. Final lot weight can also be compared to standard expected weight for an additional checkpoint.
Checkweighers can be integrated into current detection systems or function as a standalone process. Either way, the data from a checkweigher can provide additional control for the food-processing line and improve efficiencies. One single event of improper fill can mean multiple orders lost or customers parting ways with your brand. Adding checkweighing to your operations can help to save time while preventing lost revenue.