Vlasic Foods plant consolidation improves process and employee services
In an effort to reduce fixed assets and operating costs, Vlasic decided to consolidate production from their plant in Bonduel, Wisconsin to the Imlay City facility. The Imlay City facility produces 147 SKUs, consisting of "spears", "stackers", "chips", "wholes", relish, and peppers.
The project combined the purchase of new state-of-the-art cucumber slicing equipment with the relocation of pasteurizing and packaging equipment. Construction of new employee facilities, a new cucumber unloading facility, site work, new utility services, and additional automated wastewater treatment facilities were also a part of this consolidation project.
This $20 million project resulted in increased employment at the Imlay City plant of 400 people. Furthermore, the consolidation increased Imlay City's capacity by 80%, from five to nine million cases per year. The installation and de-bug occurred at the end of crop year, and was fully operational by the next crop year.
A new employee services facility was constructed, consisting of a lunch/break room area, new lockers, restrooms, and a boiler room. Adjacent to this area, a new enclosed cucumber unloading facility was constructed, including areas for cucumber cleaning and pumping (fluming) equipment. Approximately 60,000 sq. ft. of warehouse was renovated and new HVAC systems were designed and installed in each of the upgraded areas.
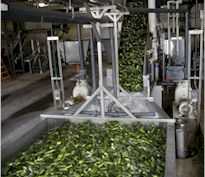
Utility upgrades included a new water cooling tower and chiller system, a new 600HP boiler system, a new 6" water main, a new air compressor and distribution system, new underground sanitary and process waste systems, and a new 15kV electrical feeder with transformer and 480V switchboard. Lighting was installed for the new parking lot and walkway, the two new building additions, and the converted warehouse buildings.
The waste treatment facility upgrade included wastewater treatment plant automation, the addition of an aeration lagoon, a phosphorus removal system, added storage capacity and discharge metering. As a result, waste screening was improved, the force main capacity was increased, and hydraulic flow capacity was improved.
The new technology installed as part of the consolidation resulted in higher quality and more consistency of the final product, as well as higher efficiencies and thus lower cost per case. Vlasic's consolidation project is "stacking-up" to be quite an improvement, in both process quality and employee services quality.
SSOE, Inc. provides a comprehensive menu of architectural and engineering services to the food industry, including the development, integration, and implementation of new and/or improved technology into existing or new products.
SSOE, Inc., 1001 Madison Avenue, Toledo, Ohio 43624. Tel: 419-255-3830, ext. 1242;
Fax: 419-255-6101.
Edited by Pam Ahlberg