Using an Integrated Process Management System to Improve Quality and Manufacturing Performance
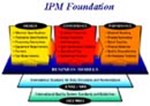
By John Wirth, Hilco Technologies
Table of Contents
ABSTRACT
TERMS DEFINED
INTRODUCTION
WHAT IS IPM?
PROJECT OVERVIEW
Business objects are organized into classes. Classes are a non-executable model element that defines basic behaviors and characteristics that are common to all objects belonging to the same class.
Modeling
Business objects may be arranged or "assembled" to create business process modeling capabilities within MES application software. This modeling functionality may then be applied in a manner that allows you to model the physical assets of a foods operation; the actual process itself within the context of S-88; the raw materials; product specifications; the quality and HACCP test specifications; and performance indicators. This capability also enables the ability to encapsulate "business rules," which are methods executed by the objects that comprise the model.
MES specific application functionality may also be created using object oriented technology. Example MES application functionality includes:
- Recipe coordination and execution
- Batch Management
- Schedule execution
- Materials Tracking
- In-Process Testing
- Lab Testing
- HACCP Testing
- Performance Monitoring
- Process Management
The modeling capability created may be applied in a manner that enables the "configuration" of MES application specific functionality from the model. This model may be configured to "encapsulate" your manufacturing standards, corporate quality policy and procedures or ISO 9000 business processes for execution within the production process.
The benefit of this approach is that it enables standardization across the entire enterprise.
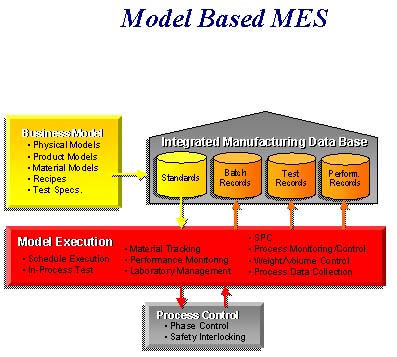
A model based MES system, utilizes object-oriented technology, to encapsulate business rules which are used to process data acquired from the process environment. The business rules or methods are used to process the raw "data" into information, which is maintained within the object. Since the business objects are always kept in context with your business model your analysis is always within the context of the way your business works.
This provides a natural foundation and excellent vehicle for implementing Integrated Process Management.
Justification
We are beginning to see a shift from "cost-driven justification" to "survival-driven motivation". Many food manufacturers view plant floor information systems as an enabler of their envisioned future state. They are faced with the challenges of new products, more products and customer-tailored products. They are changing their business to eliminate sources of cost rather than trying to survive by simply reducing costs to allow them to continue to do business in the same way. Elimination of cost is actually viewed as a by-product or second tier justification. Their primary goal is improved customer service, product reliability, reduced response time. For example, you can eliminate material cost by removing inventory capacity from all phases of production. MES based IPM allows you to remove the inventory capacity by improving the capability of the manufacturing operation. Manufacturing capability is improved as a result of in-process control of quality, quick corrective actions on non-conformances, optimal execution of schedules and improved scheduling that results from immediate and continuous feedback of performance. As you know, there are many choices regarding how to approach using technology in manufactuing systems. For this customer, the model driven MES was determined the most practical, most enduring approach in a dynamic business environment.
Approach
A pilot project scope was established that would focus on an initial line across the entire "Make" process. The objective was to introduce the technology and establish a base IPM foundation on this first line that could easily be expanded to the remainder of the plant.
It was important to establish the proper processes for use by the project team. The following were established before beginning:
- Team Mission
- Expectations clearly understood
- Project's Critical Success Factors
- Project's boundaries established
- Project's Criteria for Success agreed to
- Management's Review of the Project
- Management Escalation Process
- Schedule and Milestones Established
- Allocation of time for proper training of team members
- Communications (reporting) cycles through out the project
Critical Success Factors
The critical success factors to be addressed by the project included:
Manufacturing Performance
Material conversion costs
Quality
Reducing product defects
Reducing rework
Compliance (Quality, Process and Regulatory)
- Adherence to specifications, conformance, labeling, product/material tracking, ISO9000
Introducing new products
Safety
Product Safety (HACCP)
Change Management
Driving behaviors with real-time information
Configuring the Application
We used an object-oriented software engineering process based on S88 standards structures. The activity proceeded in a top-down approach by defining Physical, Process, and Material Models for each level defined in S88. A cross section of all the functionality required was quickly defined and prototype. The prototype provided project team representatives direct feedback on the visual representation of the model and the suitability of interfaces for associates/operators on the plant floor. The prototype was used in the training and educational program for the users.
Integrated Manufacturing Database
At the core of the system was the information repository – an Integrated Manufacturing Database. This is a configurable database that holds the physical process models, materials information, manufacturing standards and procedures, process data, key performance data (KPIs), batch history, and quality information. The database provides an S88-compliant repository of critical manufacturing information and serves as an enterprise-wide standard for consistent data management.
Business Modeling
Initially we configured a hierarchical physical model of the manufacturing plant floor in the terms and layout that are consistent with the way you think of your business. The pilot project focused on developing the model for one line covering the entire "Make" operation (from Material Receiving through Baking) and several products. The objects of the model, representing physical units of Mixer, Former and Oven, were configured with the characteristics of the equipment. The next step was to configure the process model, which represents the standard recipes for execution on the equipment, which is also represented in the model. Each standard recipe was modeled as objects by stages, operations, actions, and procedures. Additional steps involved in the modeling process include materials specification, quality testing at each stage and triggering of events, and materials management (i.e. for lot tracking). All the components of the model are actually represented in terms of the company's standard practices.
Quality Data Capture
Via data entry screens, test list management and SPC charts, application objects schedule, coordinate, measure, and record variable and attribute data values. The data screen objects present the sampled data and the resulting statistics generated from the statistical algorithms. The list manager object coordinates tests by product type and area. It prompts when tests must be completed and alarm when they are not. Operators are alarmed to out-of-specification data. SPC chart objects present data (via different statistical methods) in a graphical format. This provided the ability to do real-time interactive SPC analysis and to bring up operating procedures and corrective actions based upon run-rule violations. In the second phase this will be expanded to provide closed-loop, real-time SPC-based on rule violations by receiving messages from and sending commands to control devices. An example would be closed loop moisture control.
Batch Management
All actual product/recipe results are stored to the database as an electronic batch record or material record. The Material Record is actually structured as a control recipe and the actual results are stored within the objects. In addition, as the material moves through the line it is tracked as an object. This enables tracking all the raw materials, pre-weigh formulas and in-process materials that make up a finished product. Since the execution of the recipe is encapsulated in an object, the users can recall that object and easily access information (i.e. ingredients, times, KOVs, KIVs, tests, etc.) about the execution of that recipe.
Production Monitoring
A user interface was developed to enable users, such as managers, supervisors, and associates, real-time operational views of the execution of each standard batch/recipe; characteristics status of areas and units in the manufacturing line, and enable material tracking and batch reporting within the context of the standard batch/recipe.
Pilot System Architecture
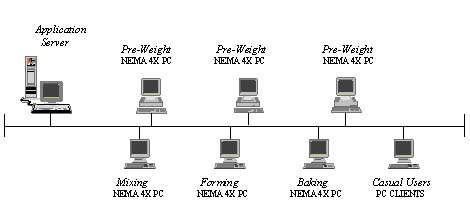
Results and Summary
Achievement of critical business success factors related to Manufacturing Performance, Quality, Safety and Change Management.
Ability to enforce standards and procedures and measure conformance to them.
Improved process visibility.
Improved product consistency and quality.
Improved yield and reduction in product giveaway.
Improved material tracking from Material Receiving through the "Make" process.
In addition the Object-Oriented MES technology had an impact by:
Eliminating IT translation of data.
Reducing system costs.
Facilitated easier/faster deployment.
Significantly reduced training.
Significantly reduced maintenance costs.
Encapsulating conformance standards.
For more information please contact John Wirth, Hilco Technologies, 3300 Rider Trail South, Suite 300, Earth City, MO 63045. Tel: 618-939-2097. Email: jwirth@hilco.com.