Turn Traceability Into Profitability With 'Vantage'
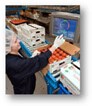
SG Systems' announced that fears surrounding compliance with the latest food traceability regulations can be ‘turned around' into an opportunity to make food manufacturing practices significantly more efficient and highly streamlined.
Dozens on ‘Vantage' users now (large and small) are reporting ROI of months and in some cases, even weeks, by eliminating handwritten lot & batch traceability records, reducing ingredient usage and reducing spoiled batches caused by operator errors during the hand scaling processes.
More and more of today's manufacturing companies are seeing traceability as a costly and unfair expense, imposed by regulators to force food manufacturing companies to conform to legislation such as the bioterrorism preparedness act, to name just one. Others see the major retailers and supermarket chains placing demands on the food manufacturing companies to reduce product recall times, provide visibility of the usage of ingredients and shipping of finished product. Many retailers and supermarkets are even going as far as to switch their suppliers due to the strength or weakness of a traceability solution implemented by the food manufacturer.
The investment to implement paper-based systems in terms of direct cost and personnel time is significant, often running into hundreds of thousands of dollars. Companies usually increase the staff levels in the QA department, who in term look to ERP companies for electronic solutions or as a weaker alternative provide a paper-based solution.
The ERP Route is problematic in terms of traceability. Their database is based on theoretical consumption of ingredients and often bears little resemblance to what's actually happening on the production floor. However, once operational, most companies appear to be reasonably content with their ERP on the surface. However bubbling under is the concern over what has become known as 'unaccountable losses'. Mention this taboo phrase to any corporate finance director and it sends a shiver down their spine. These losses usually arise from the inability of the system to access and use essential factory floor data in real-time.
The food industry is a classic example where lack of accurate real-time data is a serious problem. In such fast moving ever-changing environments keeping the finger on the pulse is critical. Consider a company manufacturing their products from pre-defined recipes. ERP systems normally work on preset targets for the batches and all their calculations assume that during the process these targets are met - precisely. Under normal circumstances they have no real-time data to contradict otherwise. For instance, if a recipe make-up calls for a target weight of say 100 lb for a particular ingredient, the system assumes that 100 lb is used; the stock is downgraded by this amount and costing calculated accordingly. However what happens if the amount used is outside the target as is typically the case? If the process relies on manual ingredient addition, more products rather than less is usually added.
This may or may not be critical to the product quality itself, but it is definitely detrimental to accurate stock management. In parallel, if a particular batch is spoilt through inaccurate additions, there may be no mechanism for bringing this to the attention of the ERP system. The first time management may be aware of these 'target excursions' is when stock checks are done and the inevitable stock inconsistencies come to light. By then it's usually too late to carry out any meaningful analysis to find out what went wrong and the 'unaccountable losses' become 'expensive reality'.
SG Systems have recognised this shortcoming and their ‘Vantage' software suite, in conjunction with their Stainless Steel workstations, already has a proven track record in bridging the gap between the factory floor and ERP. Acting as a thin client server to programs such as SAP, their solution brings a measure - control - improve ethos to the overall process- from goods-in to product despatch. ‘Vantage' is the result of extensive research together with many years of practical experience and as SG Systems General Manager explains: "In many applications we investigate, it is as though there is a thick fog permeating across the factory floor keeping critical data away from the ERP system.
Unfortunately most ERP vendors don't fully appreciate or understand the practical issues of key processes such as weighing, especially in fast moving processing environments. Of all measured parameters on the factory floor, weighing provides the most useful and crucial data throughout the process and yet in practice we find it is significantly under-utilised, even though the ROI gained through reducing wasted ingredients or overused ingredients is significant. Often the savings made from a properly installed ‘Vantage' weight based operator / ingredient control system can run into double figures by improving yields.
Real time data is essential and ‘Vantage' ensures such data is instantly available to the ERP system so that it can react to actual information rather than targets. ‘Vantage' brings true integration that continually fine tunes operational equipment efficiency. The 'improve' factor in ‘Vantage' allows processes to be optimised exactly where and when it's needed, making full use of dynamic data. This approach is highly effective in improving productivity, optimising raw material usage and minimising wastage - all important, if not obvious, factors in ensuring ongoing profitability and, above all, customer satisfaction. Traceability in line with legislation is an integral part of the ‘Vantage' concept.
SOURCE: SG Systems