4 Tips To Reduce Metal Detector False Rejects
By Melissa Lind, contributing writer
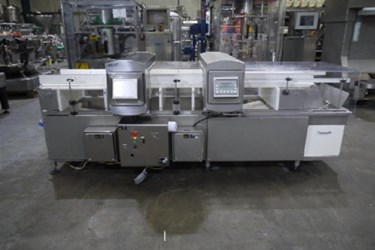
Metal-detection systems continue to be a mainstay in preventing foreign-body contamination in food production. The equipment has grown from simple magnetic and radio frequency technologies into much more complex machinery.
Today’s food industry metal detectors are capable of handling a wide variety of food products: from packaged foods to raw materials in a number of different industry sectors. With advancing technology, metal detectors are now integrated into existing processing lines with touchscreen-type applications that seamlessly mesh with data-management systems.
As technology has become more advanced, simple set and operate is no longer enough. Food manufacturers and processors must pay careful attention to the capabilities and specifications of these systems. Though set up and maintenance may be a much-less cumbersome event — no longer requiring specialized, technical personnel — improper installation can lead to a significant problem with the number of false rejects. This can significantly reduce the efficiency of the entire line, cutting down on productivity. Some issues which may result in a high number of false rejects include:
Guest Column: What To Ask When Considering Metal Detection
Conveyor System Issues
False rejects are often caused by problems with the conveyor system. Whether it is gravity feed, pipeline, or belt-based, mechanical issues in the conveyor — loose fittings, worn bearings, or improperly set metal-detector heads — may result in a high number of false rejects. To help your conveying system, ensure that all mechanical parts of the line are in good, working order and that new components are installed properly and according to manufacturer specifications.
Radio Frequency Interference
Most metal-detection units operate through a radio frequency system. In the same way that electric lines and solid structures can interfere with actual radio signal reception in AM radios, metal-detection radio waves can experience interference as well. Other equipment using similar technology in a small space may cause interference and other types of equipment may also cause improper reception of appropriate radio waves. If the wave doesn’t go through as it should, product pass through will be identified as a reject.
Product Uniformity
Some food products, meats, cheeses, and some liquids, change consistency. As the temperature and humidity may change throughout the day, products that have a high salt or water content may change in conductivity or solidity through the day. This may lead to inconsistency in terms of how radio frequencies pass through food. Changes in the rate at which radio waves are able to penetrate the food product may result in false rejects. Utilizing automatic detection technology can reduce these false rejects, but regulating environmental conditions, such as heat and humidity, is also essential.
Automatic Adjustments
Most new machinery allows for automatic adjustments, but it has to be appropriately calibrated, and turned on, to work. Manufacturers should take advantage of higher-tech settings, reducing the chance that changes in material will cause false rejects due to human failure to recalibrate or adjust.
Metal Detection Takes On New Food Safety Regulations
A high number of false rejects slows the food line, wastes product, and ultimately cuts down on profit with loss of productivity, quarantined product which can require product re-runs. In terms of employee confidence, it can have an undetermined impact on company efficiency. Metal detection can be incredibly beneficial to food-processing and packaging lines. However, reducing false rejects through proper installation and corrective maintenance is essential to receive maximum results.
Be sure to check out Food Online’s Metal Contamination Resource Center