RFID Heats Up The Cold Chain

By Bob Johns
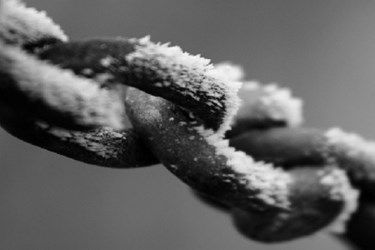
RFID is quickly becoming a go-to technology for companies that want visibility in the cold chain and are looking to improve efficiencies
The global cold chain has been growing exponentially as more perishable goods are shipped worldwide. Producers, suppliers, manufacturers, logistics companies, and retailers are constantly looking for new ways to extend shelf life or improve efficiencies along the entire cold chain. Recently, the USDA approved a new treatment process for fruits, vegetables, and other perishables instituted by Flagler Global Logistics. The new technology focuses on extending shelf life by exposing the products to a more uniform temperature. The facility uses a new filtration system that is environmentally friendly, while still helping to extend shelf life by up to one week, according to Flagler CEO Chris Scott. However, treatment processes are not the only technologies heating up the cold chain. Radio-frequency identification (RFID) has become an invaluable part of traceability and control over cold chain product.
RFID In The Temperature-Controlled Warehouse
H&M Bay, a transporter of less than truckload (LTL) frozen and refrigerated products, recently implemented an RFID solution in its cross-docking distribution center in Federalsburg, MD. According to a recent case study, H&M Bay's software development manager states, “The RFID system needed to record put away and pickups and location assignments without operator intervention.” The system also needed to be mobile, since the entire facility's workforce utilizes forklifts. Utilizing a system of RFID tags to identify warehouse slot locations, fixed RFID readers at cooler and freezer doors, rugged mobile RFID readers mounted to each forklift, RFID-tagged pallets, and mobile rugged computers, every pallet is tracked throughout the facility. By removing the need for manual entry by operators, the RFID system has led to a 25 percent reduction in cross-docking labor, along with the ability to track product in the temperature-controlled areas in real time. Alert capabilities are also being utilized in case product is placed in the incorrect temperature zones, and an increase in freight transfer speeds.
Learn about the impact of big data within the cold chain
TomTom Business Solutions recently began to integrate fleet management data and mobile printing. Utilizing RFID labels printed directly from mobile devices, individual products or pallets can be tracked throughout the entire cold chain. Cold chain distributors will be able to print receipts detailing temperatures from processing to delivery by GPS positions. At any time, a customer is able to verify delivery, audit temperatures along various points during delivery or storage, and ensure product was not stored longer than stated.
Benefits Of RFID In The Cold Chain
There are many benefits to using RFID in the cold chain:
- Ability to track inventory throughout the chain
- Comply with PTI (produce traceability initiative)
- React to real-time data such as temperature fluctuations or prolonged storage
- Reduced labor time through the reduction or elimination of manual tracking
- Access to data such as light exposure, humidity, temperature, movement, or other environmental criteria provided by the location
- Ability to track individual pallets in real time in the event of a recall or possible contamination
With so many companies sourcing globally, it is extremely important that product be stored properly, traceable, and moved efficiently to reach its final destination with as little spoilage or damage as possible. RFID is continuing to emerge as one of the best technologies to aid companies in reaching this goal and maintaining margins.