Reduce Costs And Energy By Optimizing Pumps
By Isaac Fletcher, contributing writer, Food Online
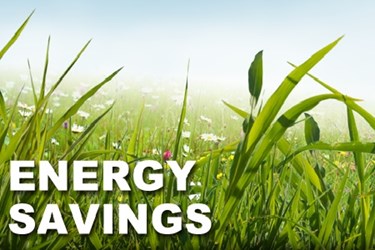
With climbing energy prices and growing concerns over environmental impact, now is the perfect time to explore methods for reducing energy costs throughout your food-making operation. Pump optimization is a great place to start.
If you are looking for ways to cut costs and reduce energy consumption in your operation, then pump optimization is an important consideration. Producing viscous, pumpable products requires considerable amounts of energy, and a sizeable portion of that is spent running pump systems. By efficiently and effectively optimizing these pumps, you can significantly reduce energy consumption and cut related costs.
Although pump optimization is not a new concept, the fiercely-competitive landscape of the food industry makes it highly relevant in today’s market. By using the right pumps, you can reduce total cost of ownership, increase system performance, and lower your company’s environmental impact.
The Cost Of Energy Consumption
Over the course of a pump’s life, capital costs account for only a small portion of overall costs. For example, a centrifugal pump’s overall cost during its life is made up of roughly 6 percent initial purchase, 4 percent maintenance, and a whopping 90 percent energy costs required for operation. Reducing the power required to run the motor can have impacts in the following areas:
- Installation Costs — the size of the pump motor influences all related electrical components including circuit breakers, frequency inverters, and cables.
- Running Costs — selecting the right pump and designing it for Best Efficiency Point (BEP) can greatly reduce the amount of energy needed to run the pump system. Less energy consumption results not only in lower operating costs, but also in a reduction in the amount of heat the pumping system emits. If your product is heated up during a stage of production it is not supposed to be, you will have to face additional cooling costs and further energy expenses.
- Product Quality — pumps that run at low levels of operational efficiency add unnecessary stress to products. For example, in dairy products, increased shear rate and added stress prior to pasteurization can increase the risk of free fat. Additionally, when producing yogurt products, the shear rate and stress will lower the viscosity of the product, thereby degrading its quality.
The Best Efficiency Point
The BEP, mentioned above, is the point at which a pump runs at optimal head and flow rate, delivering the highest-efficiency possible for the given task at hand. The closer the BEP is to the required duty point, the higher the overall efficiency at which the pump will operate.
Reducing Pump Energy
The benefits of reducing energy inputs for pump operation are clear, but the way to achieve energy reduction may not be. An important first step is performing audits on existing systems and adjusting pump operations to restore or increase efficiency. Even minor alterations can have a noticeable impact, so continuous evaluation and modification is the key to optimization. Some things to consider are:
- Changing pumps so they operate at their respective BEP
- Implementing variable frequency drives to lower energy costs
- Altering the diameter of the pump impeller
- Reconfiguring your pipe layout
Looking for more information on energy savings with your pumps? Click here.