Leveraging APM Technologies Can Improve Your Food-Processing Operations
By Isaac Fletcher, contributing writer, Food Online
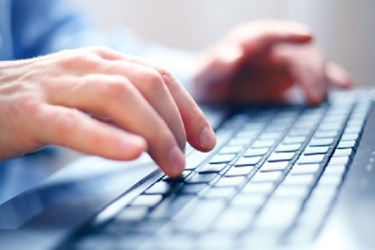
In a business environment as competitive as that of the food and beverage industry, manufacturers of all sizes are seeking ways to carve out a competitive edge. Ensuring that plant assets are being used to their full potential is a necessary part of remaining relevant in the market.
In order for your food or beverage manufacturing plant to run at optimal and efficient levels, it is critical to be well informed about the performance of your plant assets and be able to make precise calibrations when necessary. When it comes to monitoring and managing the performance of your processing plant, there are a handful of key asset performance management (APM) technologies that your plant needs.
APM Software
You may have considered APM software for your processing plant before, but have been discouraged by high prices. For smaller organizations working under a limited budget, the cost of APM software implementation can often be too high of a barrier to overcome. However, with advancements in cloud computing and a shift in revenue models, many smaller companies are now able to gain access to APM software on a subscription basis as opposed to the high-cost, upfront, initial investment of the past.
With the current rate of technological proliferation, there are many potential avenues that smaller manufacturers can use to gain access to APM software applications. Affordable solutions can yield a significant ROI when the software is properly leveraged to support processing plant operations.
Safety Calibration
The production of food and beverages requires strict attention to safety; especially as the FDA tightens regulations and ISO 22000 standards are revised. To meet strict food and beverage safety requirements, manufacturers need to ensure their ability to monitor quality, safety, and sanitation is up to par. Failure to adequately meet safety requirements and provide proper documentation can result in production stoppages, recalls, and fines.
Accordingly, calibration applications are an important part of your plant’s APM toolkit. Equipment that is used to monitor quality, safety, and sanitation needs to be properly calibrated to ensure it is running optimally, and efficiently. Manual calibration is tedious and any operator errors can result in high costs and lost product.
Reducing Risk
As mentioned, updated and more stringent FDA regulations mean an increased focus on food safety and the failure to meet safety standards can be extremely cost. Consumer safety needs to be a top concern and it is essential to have proper technology in place that helps reduce the risk of food-safety issues. APM technologies can be instrumental in complying with stringent standards and remaining competitive in the marketplace. Tools, such as failure modes and effects analysis (FMEA), can be efficiently utilized for risk assessment and detecting problematic areas so that they may be addressed before an unsafe product goes to market.
Water Use
A key factor in promoting cost-effective operations is reducing the amount of resource inputs needed during production. Within the food-processing industry, water consumption represents a large expense as it is necessary for many areas of processing, cooling, sanitation, and packaging. APM applications can assist manufacturers in reducing water usage by using sensors to monitor operations and collect data. This data can then be used to highlight times of peak usage. Once data is collected and presented, manufacturers have the tools necessary to improve water efficiency in key operational areas.