Key Technology Introduces CIT Hyperspectral Imaging Module For ADR 5 To Detect And Remove 'Sugar End' Defects From Potato Strips
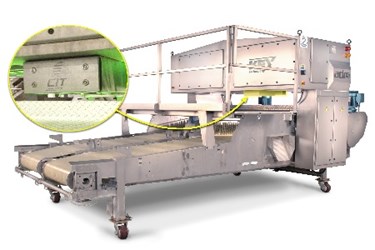
Key Technology introduces hyperspectral imaging on its popular ADR 5 automatic defect removal system for potato strips. Featuring Chemical Imaging Technology (CIT), an advanced value-added hyperspectral solution that evaluates the chemical composition of objects, CIT detects “sugar ends,” an invisible defect that plagues potato processors, which the ADR then cuts from the wet strips, along with all other defects, to recover the good product. ADR 5 with CIT detects and removes sugar ends and other defects from potato strips to improve product quality while maximizing yields.
Key’s new CIT hyperspectral imaging module is available as an option on new ADR 5 systems and as an easy-to-implement in-field upgrade for installed ADR 5 systems.
“As the world’s first hyperspectral imaging solution for potato strips, ADR with CIT brings sugar end detection to the point on the production line that can remove this troublesome defect without losing yield. ADR with CIT cuts the sugar end defect from the strip so only the defect is lost, unlike whole potato sorters with hyperspectral imaging that cause the entire potato to be redirected,” explained Marco Azzaretti, Advanced Inspection Systems Product Manager at Key Technology. “Compared to other methods being used by potato processors to manage sugar ends, ADR with CIT is the most economically efficient, preventing costly disruptions to the production process. Recognizing the enormous value in this approach, a major potato processor has already placed an order for the first system.”
The new CIT module is additive – the ADR’s previous performance, including detection capabilities and throughput, remains unchanged while sugar end removal is added. The new CIT hyperspectral module detects sugar end defects while the ADR’s Vis/IR cameras identify green defects and differentiate between potato peel and brown defects such as bruises and rot, enabling ADR 5 with CIT to detect and remove the widest range of defects on both peeled and peel-on potato strips. ADR 5 handles strips from thin shoestring to thick steak-cut French fries, automatically cutting out defects at production rates of up to 16,200 lbs. (7.4 metric tons) per hour.
Sugar ends, also referred to as dark ends, glassy ends, translucent ends, and jelly ends, is a physiological tuber disorder caused by environmental conditions. Potato strips made from sugar end potatoes exhibit undesirable dark brown areas after frying, caused by the higher concentration of reducing sugars caramelizing. The challenge is that sugar ends are invisible to traditional detection technology until after the product has been thoroughly fried, so potato strip processors can be unaware they have a sugar end problem until their foodservice customers fry the strips and complain.
The new CIT hyperspectral imaging system successfully detects sugar ends prior to frying. CIT is a proprietary solution developed by EVK and Insort that utilizes unique software and algorithms to process information from powerful broad-spectrum hyperspectral sensors and evaluate the chemical composition of potatoes. In July 2013, Key entered into an exclusive licensing agreement to deploy CIT in its products to enhance the value of its potato sorting capabilities.
“By marrying CIT with ADR, the operational benefits are maximized since the ADR system cuts the defects from the wet strips and recovers good product to optimize product quality while minimizing yield loss. Developing a CIT hyperspectral module for ADR 5 is an important step in improving the economics of successfully managing the occurrence of sugar ends,” added Azzaretti. “We’re also working to integrate CIT with other Key digital sorters to deliver new value-added solutions to our strategic partners in the potato industry.”
For more information on Key’s ADR, visit www.key.net/products/adr.
About Key Technology, Inc.
Key Technology is a global leader in the design and manufacture of process automation systems including digital sorters, conveyors, and processing equipment. Applying processing knowledge and application expertise, Key helps customers in the food processing and other industries improve quality, increase yield, and reduce cost. An ISO-9001 certified company, Key manufactures its products at its headquarters in Walla Walla, Washington, USA and in Beusichem, the Netherlands; Hasselt, Belgium; and Redmond, Oregon, USA. Key offers customer demonstration and testing services at five locations including Walla Walla, Beusichem, and Hasselt as well as Sacramento, California, USA and Melbourne, Australia; and maintains a sales and service office in Santiago de Queretaro, Mexico.
Source: Key Technology, Inc.