Juice Manufacturere Improves Production And Product Quality With Opcenter APS
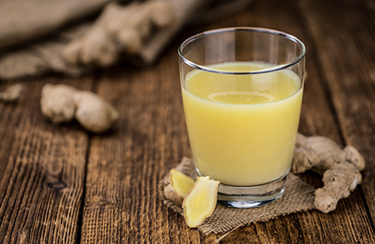
Generating accelerated demand
Natural One is a Brazilian company that offers a unique, 100 percent natural real-juice product that preserves the flavor of each ingredient, which is produced from fresh fruits and vegetables. This required years of collaboration with technology partners from Germany, the United States, France, Netherlands, Japan and Sweden, who helped Natural One design and implement a cold aseptic filling plant, which ensures all the characteristics of the fruits and vegetables are maintained.
The company offers the market more than 60 items divided into two product lines: refrigerated chain and shelf-stable chain. The refrigerated chain is made with ingredients that need refrigeration to maintain all its freshness, flavor and nutrients, and the shelf-stable chain is made with less sensitive fruits and vegetables that maintain their nutritional characteristics without refrigeration. The products are offered in 300-milliliter (ml) bottles up to two-liter (L) bottles.
Natural One’s product quality has generated accelerated demand growth in recent years and has enabled the company to reach international markets. In addition to Brazil, where they can be found at around 40,000 points of sale, its products can also be found in 12 countries, including Chile, Singapore, the Philippines, Colombia and China.
A complex equation Year after year the demand for Natural One quality products grew more than expected. Serving this growth by using only one filling line became a huge challenge. The first issue was to improve the performance of the line, which was being used at about 60 percent of its capacity. A large part of the installed production capacity was lost due to carrying out the setup, especially those necessary for changing the type of packaging, which requires the line to remain idle for six to 10 hours.
Siemens solutions enable Natural One to improve production and product quality. Using Opcenter APS to reduce production planning process from three days to two hours with greater reliability.
Get unlimited access to:
Enter your credentials below to log in. Not yet a member of Food Online? Subscribe today.