Hygienic Equipment Design Helps Combat Pathogens
By Isaac Fletcher, contributing writer, Food Online
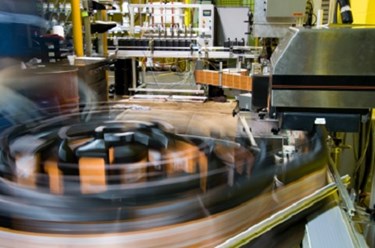
In a collaborative effort, the Alliance for Innovation and Operational Excellence has established a set of critical guidelines aimed at helping consumer packaged goods companies and suppliers create a standard for hygienic equipment design
One of the main problem areas for pathogen growth in low-moisture food production environments is the equipment that is used to create the product’s primary packaging. Consumer packaged goods companies (CPGs) and suppliers have a commitment to create equipment that can be easily cleaned, sanitized, and returned to production with minimal downtime. In order to achieve this, CPGs have a few options. Although having multiple options is generally beneficial, this variety of options for packaging equipment often leads to one-off designs for each CPG when a standard equipment design could actually be more effective.
The Alliance for Innovation and Operational Excellence (AIOE), founded by the association for packaging and processing technologies, PMMI, helps bring CPG production and engineering professionals together with suppliers in an effort to address main areas of concern. One such issue is the need to consider hygienic equipment construction for low-moisture foods.
Tom Egan, V.P. of industry services for PMMI, explains that the resulting document, One Voice for Hygienic Equipment Design for Low Moisture Foods, “will help numerous companies reduce one-off designs by utilizing a framework, including risk assessment, to determine equipment design for wet and dry clean environments.” Underscoring the importance of risk assessment in process design decision making, Egan goes on to say, “The risk assessment integrates with hygienic zones to arrive at a ‘must have’ criteria that are applied to several existing hygienic design guidelines.”
With regard to design decisions, Egan explains that, “The CPGs can still select a more rigorous OEM design, but the One Voice process lays out the base-level criteria, saving time and investment throughout the purchase discussions and decisions. This process enables the operations team to inform upper management of the choices made and the assessment that led to the design choice.”