High-Tech Cocoon Provides Thermal Efficiency for Cold Storage Plant
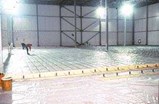
By George Mathis, Insulated Structures & Systems
and Ed Dougherty, Ben Pekin Corporation
Table of Contents
Designing a modern cold storage facility
Designed for high R factor
The insulated cocoon
The siding
The flooring
Preventing permafrost
The roofing
Protection of incoming trucks
The refrigeration penthouse
Into operation
Frozen product from all over the world arrives at East Coast ports such as Philadelphia, Baltimore, Wilmington and Newark. From there, it travels by refrigerated truck all over the Eastern Seaboard. Southern New Hampshire was badly in need of a large new public cold storage warehouse for handling short-term storage and redistribution of domestic and offshore commodities in transit.
Production companies, food processors, manufacturers and importers all asked for a new facility to handle frozen foods, ice cream, and chilled products like seafood, meat and poultry. Londonderry, New Hampshire, the selected site for the facility, is located close to Nashua and Manchester, within convenient reach of all of southern New Hampshire. It is just two miles from exit 4 on Interstate 93, a gateway to northern New Hampshire and northern Vermont.
Designing a modern cold storage facility
The Londonderry Freezer Warehouse LLC is located on 10 acres of land. The building has a 62,410-sqft footprint, and an area of about 1.6 million cubic feet.
The warehouse is, essentially, an insulated cocoon. The single building contains a -20°F area for ice cream storage -- presently set at 10,000-sqft, but readily expandable or reducible as distribution warrants. Frozen fish and other foods are held at -10°F, and chilled foods at 35°F.
The working truck dock is also held at 35°F, providing a vestibule for the freezers, helping to keep heat infiltration to a minimum, and ensuring that product is always handled under controlled temperature conditions.
From the dock, forklifts move the product as desired: to the freezers, or to a mezzanine repacking area within the dock, which is also held at 35°F. The refrigerated trucks back into dock shelters for loading and unloading. This building is designed with a cantilevered wall creating an overhang at the dock, which acts as a canopy for the trucks while maintaining a clean architectural appearance to the building.
Designed for high R factor
The refrigeration system for a cold storage warehouse is, of necessity, designed for the highest expected ambient temperature for the locale. The Btu capacity of the building, anticipated usage, and the energy rating of the insulating materials are also integral considerations. A hefty insulating ("R") factor was desired to minimize the high cost of energy for refrigeration.
The refrigeration system and insulation materials are accordingly over designed for the southern New Hampshire area, with the goal of economic operation. The system will accommodate 100°F ambient outside air, and the refrigeration and thermal insulation are specified to maintain the entire building at -20°F if needed.
The insulated cocoon
In designing the building and specifying materials of construction, good insulating products and good insulation techniques were of major importance. The insulated cocoon is, in essence, an envelope ensuring continuity of insulation. Walls, floor and roof are all thermally connected.
The building's structural steel frame is erected on a concrete slab foundation. The steel columns are not, however, set into or onto the concrete. Each steel column is erected on a wood block for thermal isolation.
Siding, roofing and flooring are primarily composed of insulating materials.
The siding
The siding, rated R-40, is composed of 5-in of rigid foam insulation, foamed-in-place over steel faced panels. The panels were pre-manufactured for installation at the job site. In the completed building, the steel panels face the warm outside, and the insulation, with a lightweight metal skin, faces the steel flange on the cold inside.
The siding panels are protected inside the plant with concrete curbs. The outside is surrounded with an asphalt berm and protective concrete-filled steel bollards.
The flooring
On top of the concrete slab foundation, the flooring is Owens Corning Pink Foamular 400 extruded polystyrene insulation board, with a compressive strength of 40 psi -- an especially strong, tough and resilient material, which will maintain its dimensional stability despite the constant pounding from forklift truck movement.
The material's high resistance to moisture absorption, the result of its light, closed cell construction, assures retention of its R-value of 5 per inch of thickness. The rigid foam is lightweight, durable and impact-resistant.
The 6-in thickness of the insulation provides a thermal value for the floor of R-30.
Preventing permafrost
Somewhat surprisingly, with all the attention to building refrigeration within the building, underfloor heating is also provided. A huge building cube on a concrete foundation, if maintained year-round at temperatures below freezing, would eventually create a great deal of moisture. Permafrost would occur, possibly causing the building to heave.
To prevent permafrost, an underfloor piping system circulates glycol, which carries waste heat from the refrigeration system at about 50°F.
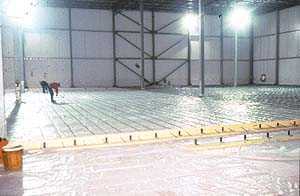
The roofing
The structural steel includes bar joists to support the roof: a series of V-sections of steel allowing good circulation of refrigerated air. A lightweight steel deck is pitched slightly from parapet wall to end drains.
Foamular ThermaPink roofing insulation rated 25 psi, was selected for the roof. Some 850,000 board feet were utilized -- about 22 truckloads of the extruded polystyrene material. Nine inches of this insulation were used on the roof, for an insulating factor of R-45. The 3-in thick ThermaPink insulation boards were installed with joints staggered by half a board (4-ft) in both directions to avoid air infiltration. The loose-laid insulation was covered with a single-ply membrane, followed by stone ballast.
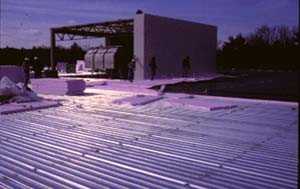
The Londonderry facility represents one of the first times that extruded polystyrene insulation has been used for the roof as well as the floor. Foamular and ThermaPink were selected for reasons of economics, the convenience of a single supplier for roof and floor insulation, and the ability of the single product to completely meet requirements for roof and floor insulation. The ThermaPink Owens Corning product is the first extruded polystyrene board to be approved by fire codes for use directly on the metal deck.
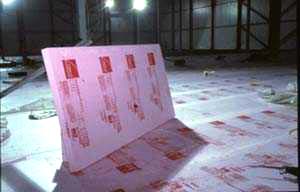
BOCA ES and SBCCI PST and ESI have accepted UL test methods as a valid measure of underdeck fire spread performance and have issued technical reports to that effect. The reports were released under typical building code evaluations that allow the introduction of new methods and materials when proper engineering and life safety justification is provided by the applicant. A third US model code agency, ICBO ES, is reviewing the matter1.
Protection of incoming trucks
Above the loading dock side of the building, a cantilevered metal insulated panel overhang serves as a canopy over the trucks to keep the loading end dry.
The refrigeration penthouse
Located in the center of the essentially flat roof, a penthouse contains the fan coil evaporators that generate refrigeration for the warehouse with ammonia piped from the central refrigeration compressor rooms. To facilitate free flow of cold air, just a grated floor separates the penthouse from the main storage area. The penthouse is at the same temperature as the area it cools.
No equipment projects below joist level, avoiding any possibility of collisions with forklift trucks.
Into operation
The entire warehouse project, from finding the site to completing the facility, took about a year. Actual construction began in October 1997, and the Londonderry Freezer Warehouse was down to temperature and accepting product by mid-May of 1998.
For a commodity-conscious public, the warehouse will facilitate quick shipment and ensure properly controlled temperature for transit and storage. In an era of high-energy costs, the thick, thermally efficient insulation and savvy design and installation ensure optimum energy efficiency for the new cold storage plant.
About the authors
George Mathis is president of Insulated Structures & Systems, Inc. He has worked in the design and construction of cold storage facilities for more than 40 years, in Russia, Saudi Arabia and Ireland as well as the U.S. & Canada.
Ed Dougherty represented the owner, developer Ben Pekin Corporation of Chicago, during the construction of the warehouse. When the project was completed, he became its operations manager. Dougherty has been operating cold storage warehouses for twenty-three years.
1. THE CONSTRUCTION SPECIFIER, February, 1997.