From Sticky To Crumbly – Securing Product Quality
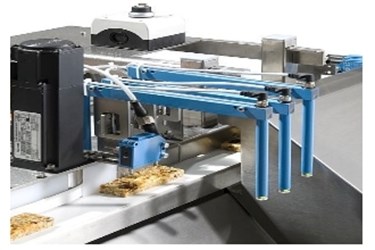
The saying goes that it’s the little things that count. However, life’s delighting pleasures such as delicate biscuits, cookies or wafers can become disappointments if a consumer opens a package only to find crumbs. These fragile foods can easily crumble and thus need extra-gentle handling already during the packaging process in order to provide consumers with the product quality they expect. On the other hand, chocolate tablets and sticky products like muesli bars are strong enough to withstand some impact of packaging machinery, but their characteristics require special handling of a different sort. As a result, manufacturers of those kinds of foods need to choose wisely when considering inline feeding to ensure their products are packaged without damage.
What’s more, these days new food items are entering the market at a rapid pace. Different products require different packaging formats to stand out at the point of sale. As a result, food manufacturers require horizontal packaging solutions that are flexible in order to make quick product changeovers as needed. The utilized inline feeders need to work seamlessly with horizontal flow wrapping equipment for maximum efficiency.
Fortunately, packaging technology is available to meet these demands. Inline feeders can address these needs and enable greater packaging flexibility. For example, Bosch Packaging Technology B.V. offers a portfolio of modular infeed technologies specifically designed to handle delicate baked goods and other fragile items. With food products becoming ever more diverse, making sure manufacturers employ the right packaging system to address their needs requires expertise.
Here are some tips on technologies that help meet confectionery, biscuit and wafer manufacturers` packaging challenges.
Not all biscuits crumble equally
To package fragile items on a horizontal flow wrapper, a feeding system must be gentle and limit impact on the product. A good example is delicate biscuits that have different shapes and sizes or various densities. Simply put, each biscuit crumbles differently. Depending on moisture content and other factors, some are more resistant to crumbling and can endure higher levels of impact during packaging. Others have more crumbly characteristics, like crackers, and are more delicate and prone to breakage.
For biscuits that are less prone to crumbling, magazine feeders, also known as gravity hoppers, offer excellent and cost-effective options. The products can be fed both manually and vibratory into the flow wrapper. As gravity hoppers can be easily adjusted to different heights or shapes, manufacturers benefit from the flexibility of the feeding solution to package single products as well as items in groups or stacks.
To help ensure that more fragile, “cracker”-type biscuits do not crumble during packaging, indirect gravity hoppers offer a solution. Thanks to the pushers that bring the items into the machine chain, there is a limited impact on the product. Manufacturers benefit from extra-gentle product handling. The recently launched product stacker collator (PSC) from Bosch Packaging Technology is a feeding solution that gives manufacturers the flexibility to package multiple stacks in-line with low impact. The system utilizes a variety of carrier heights to lift products and place them onto static shelves, creating multipacks up to five layers high. These stacks are then transferred to horizontal flow wrappers to be wrapped.
Avoiding sticky situations
Chewy products like muesli bars present their own challenges. Foods and snacks made with honey and other viscous ingredients can stick to each other when transported to the horizontal flow wrapper, making them difficult to handle. Because of their stickiness, muesli bars and chewy granola products would require considerable force to separate them before they get packaged. For such foods a contactless feeder is ideal because it avoids any physical contact between the products. Products come in separately from smaller belts, and instead of buffering, the belts directly position products into the packaging machine chain.
Wafers also have the tendency to stick to each other, however moderate force is usually enough to separate them. Adding to this challenge is the fact that retailers often want such products to be packaged in multipacks, with products stacked or placed behind or next to each other. A flexible and modular infeed system allows manufacturers to package wafers either lengthwise or transversely into the package. Modular infeed systems can be set up to use a cross belt feeder in which plates push products at a 90-degree angle; this enables wafers to be wrapped short end leading. If the wafers are fed lengthwise into a package, an inline grouping module is recommended. The products are buffered long side leading forming a group, while an overhead belt stopping the products creates a gap between the individual groups. With those options, manufacturers can benefit from the possibilities Bosch offers to package sticky products.
Without a scratch
Chocolate bars can be distinct. Even “plain” chocolate bars are adorned with elaborate and decorative lines that are the hallmarks of the chocolate brand being consumed. These decorations pose considerable packaging challenges.
Chocolate has an exceptionally smooth appearance and consistency; therefore, from the time it is brought from the moulding line to its final packaging, any scratches can be easily detected. When packaging chocolate tablets, it is important to regulate the buffer forces in packaging equipment accordingly so they withstand it. This can be realized by using multiple belts.
Not all chocolate products require the same type of feeding. In cases where scratches are not obvious on the product, for example on a multilayer chocolate bar, a cross belt feeder could be the right solution. Cross belt feeders are ideal for rectangular products like chocolate bars as they deliver products at obtuse angles, providing a continuous infeed flow into the packaging machine.
It’s all in the feeding
Delicate products require delicate handling, and choosing the right feeding solution is crucial for manufacturers. While there are some general parameters in choosing the right feeding equipment, given the vast diversity of food products and packaging needs, the best solution requires consultation from experienced packaging professionals. It’s self-evident to choose a packaging system with a conveyor belt layout that fits the properties of the product. Manufacturers are recommend to decide for a system including top and side guides that adjust easily and rapidly, and which performs a full range of functions such as turning, grouping, buffering, stacking, and cardboard feeding.
The right feeding solution helps ensure that products reach the consumer with the quality and attractive appearance expected. The appropriate system also gives manufacturers flexibility to adjust and optimize packaging processes depending on what is packaged. Choosing a modular system that enables easy changeovers, low maintenance and easy cleaning will help packaging productivity, while protecting manufacturers brand’s integrity.
Source: Bosch Packaging Technology