Fortress Technology Announces Digital Quality Control Program For Metal Detectors In Food Manufacturing
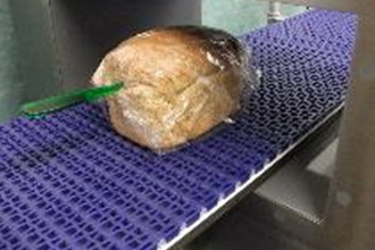
Metal detectors are an integral first step in food safety. However, proper management with regular testing of inspection systems is vital to ensure optimum protection is achieved. To provide food manufacturers with a reliable, accurate and auditable testing procedure, Fortress Technology has unveiled the latest version of its Halo digital testing. Available on Fortress’ full range of digital metal detectors, including the Vertex for snack food inspection, the self check software is a failsafe and cost effective solution to ensure your system is meeting quality control standards.
To successfully comply with the Global Food Safety Initiative (GFSI) and Hazard Analysis and Critical Control Point (HACCP) production standards, it is important for food manufacturers to have an appropriate and effective testing system established for the audit process of industrial metal detectors. Depending on the criteria set out by each retailer Code of Practice (COP), tests are typically scheduled throughout the day at hourly intervals to confirm the inspection system is repeatedly identifying all potential metal contaminants.
However, regular checks that are carried out manually can be a drain on resources. This is particularly true when testing metal detectors is made difficult due to access, machine position, product flow and environmental conditions. This is where Halo digital testing comes in. Guaranteed to save food manufacturers time and money, Halo automatically and independently checks for all metal materials - ferrous, non-ferrous and stainless steel. Systems fitted with feedback sensors will also check the reject operation, including confirmation that the reject system is working, the flow and fullness of the reject bin.
Available on gravity metal detectors that inspect loose or free-falling snack products and ingredients, the latest Halo software release from Fortress provides valuable protection for pretzel, nuts, popcorn, cereal and corn and potato crisp brands. In addition to reducing operational costs, digital testing also reduces waste and product rework.
Time Is Money
Up until now, metal detectors had to be manually checked every hour for QC compliance. However, the cost of running these tests by hand on such a regular basis can be high. Rather than relying on operatives to schedule, perform, document and submit inspection checks, Halo digital testing automates the timely aspects of the process, allowing food manufacturers to tackle this drain on resources and save thousands of dollars each month.
Additionally, reducing the frequency of manual testing helps to eliminate the risk of human error and workplace injury at critical control points on a manufacturing line. Fortress President Steve Gidman explains: “Manual tests on metal detectors handling free-falling products, those fitted above bagging lines or ones processing bulk products are challenging. They can be difficult to reach, in many cases need two people to complete the test and incur production loss while each test is completed.”
Additionally, the recommended test point on a detector is the very center of the aperture where the signal is least sensitive. However, it’s impossible on a vertical line, for example, to manually drop a test sample into the center of the detector, which can result in data records showing inconsistent signal variations.
When specifying Halo on a Fortress metal detector, the QC test is completed with 100 percent accuracy by generating signals to disturb the magnetic field exactly as a metal sphere in the center of the metal detector’s aperture would. The check result shows the size to be exact, as if a real piece of metal passed through the detector in the weakest point in the aperture.
With electronics and transmitting coils separate from the metal detector, Halo gives manufacturers a true measure of how each metal detector is performing, removing the risk of human error while providing a reliable and detailed audit trail. This all happens on the fly with minimal impact on production, which means that production will not stop while the test is in progress. The line will only halt if the metal detector or reject checks fail.
Managing And Maintaining Important Data
There are two major components of a metal detector GFSI audit: the physical inspection of the machinery and a documentation review. Routine testing results are a significant part of this. By utilizing Industry 4.0 principles, Halo digital testing gives snack firms the flexibility they need to manage and maintain important data.
Users determine how often the system completes QC tests and how the validated test data is digitally saved for audit purposes.
By incorporating all of these innovative features, Halo digital testing captures all the data required to meet audit requirements and guarantee QC compliance and control. Steve ends: “Payback for a new Fortress metal detector fitted with Halo digital testing is typically less than 12 months. Utilizing the latest digital software advancements, snack manufacturers can be assured of a failsafe, reliable system that guarantees test data on food processing and packing lines is accurate, consistent and reliable.”
About Fortress Technology Ltd
Fortress Technology Ltd. is a privately-owned Toronto based company. Fortress Technology is the only metal detection manufacturer that, since its inception in 1996, custom manufactures metal detectors to suit its customers’ needs, application and specification while ensuring optimal performance. Dedicated to their Never Obsolete Commitment, new technology is developed to be backwards compatible and accessible without having to purchase an entirely new system. Renowned in the industry for their speed, accuracy and simple operation, Fortress systems are used widely within a range of food industry sectors including bakery, meats, ready meals, dairy, confectionery, fresh foods, frozen foods. In addition to product manufacture, the company offers a range of before and after sales service and support services including consultation, product testing, training, preventative maintenance plans, spare parts and validation visits. Fortress is a global enterprise providing worldwide coverage from its manufacturing facilities in Canada, the UK, and Brazil. For more information, visit www.fortresstechnology.com
Source: Fortress Technology Ltd