Ensuring Foreign-Body Detection Systems Are Up To Par
By Melissa Lind, contributing writer
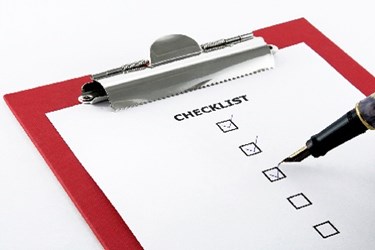
No matter what type of foreign-body detection being used on your food-processing line, performance testing must be completed to ensure that system is working. Testing will help ensure that contaminates are identified each and every time they occur.
Verification testing should be done on a routine basis for maintenance purposes, but also at any adjustment period as well as for-cause investigations. These tests must confirm that foreign-body contaminants in food products are detected within set specifications and that when positive results are identified, appropriate warning notification and separation mechanisms are employed.
Verification testing should be performed with worst-case scenarios in mind. This means that detector testing should be under the most-challenging conditions that may be seen in your food processing line. Worst-case conditions include:
- Contaminant Types — Testing should use both contaminant types that are easily identified and types that are more difficult to identify due to size, structure, or material.
- Contaminant Positioning — Testing product-inspection systems should be completed with known contaminants. These contaminants should be place at the physical point in the detection system where it is most likely to be missed. In many systems, this is the exact center.
- Contaminant Position Within Food Product — It is important to place known contaminants inside product in a position they are least likely to be identified. This may be in the corners of packaging or near other, hard ingredients of the food product.
- Speed — Testing of product-inspection systems should be done at varying speeds, from low to the highest-speed or most-productive scenario. If two lines are normally run, testing with both lines running is essential.
- Multiple Positives — Verification testing should include identification of multiple, repeat contaminations. When warning or separation thresholds have been met, inspection systems can’t lag; they must continue to identify contaminants in products following a positive screen.
Commercially-available testing bodies are a good option for verification testing. These are available in ferrous, non-ferrous, and stainless steel spheres of varying sizes that can be placed exactly where you want them to be in the product. Other types of sample contaminants, such as high-density plastics material types, are also available. These should be chosen based on the most-likely type and source of contaminants in your unique food-processing line. Testing contaminants should ideally be placed within the product you are processing, but care must be taken to identify which packages are strictly for testing purposes so that they do not enter the market.
Verification testing should be performed on a routine schedule with the most likely testing points being:
- Shift changes
- Product changes
- Lot or batch completion
- Machine adjustments or re-calibration
- Line stoppages
- Other pre-determined testing time points
- Any known or suspected lapse in detection efficiency
Verification of foreign-body contaminant detection should involve a minimum of three test runs for each condition. For routine performance testing of well-performing equipment, one test for each condition may suffice.