Design Considerations For Low-Pressure Air Blowers In Wastewater Treatment
By Paul Petersen
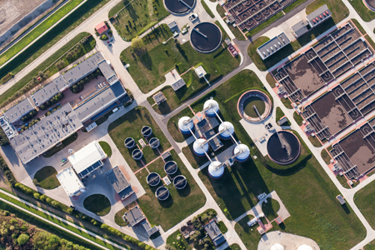
The basic function of a wastewater treatment (WWT) system is to accelerate the natural process that purifies water. And low-pressure air blowers are used in WWT for two key purposes that help accomplish this goal: aeration and agitation.
Aeration provides usable oxygen for the purification process. This enables much higher levels of aerobic microorganisms (called “bugs” in the industry) that remove waste from the water more quickly than would occur naturally. Agitation is a stirring process in the water that keeps the material needing treatment suspended and better available to the bugs so that they can make use of it and remove it from the water stream.
Below we provide an overview of the role of low-pressure air blowers in the design of industrial and municipal wastewater-treatment systems.
Starting Point For System Design
The successful design of a blower system for wastewater-treatment depends on several considerations:
- Flow (in SCFM) and pressure (in PSI)
- Site conditions (ambient pressure, temperature of operating environment, available space, indoor or outdoor, climate, etc.)
- Turndown (variation between real-time and maximum flow)
- Redundancy requirements (due to the critical nature of the WWT process)
- Costs (initial capital investment and long-term cost of operation)
Let’s take a look at each of these categories.
Flow And Pressure
Flow is a function of the demand for oxygen of the bugs used in the treatment process. WWT actually involves two separate processes, both of which require oxygen:
- Metabolism of bio-organic materials, such as biowaste in a municipal WWT plant, food particles in food and beverage processing, wood materials in a paper plant, or fibers in a textile mill
Waste + Bugs + O2 = CO2 + NH3 + Energy to Produce More Bugs
- Removal of ammonia occurring in the waste, and also created by step 1 above
NH3 + Bugs + O2 = H2O + NO3 + Energy to Produce More Bugs
Taking wastewater samples and calculating the biological oxygen demand and ammonia levels helps engineers determine the system’s air demand. Note that this is a mass flow that varies with ambient temperatures, since higher-temperature air has less oxygen.
It’s important to understand that a blower doesn’t create pressure like an air compressor does. A blower creates flow. A blower’s pressure rating, such as 15 psi, is really a rating of the maximum backpressure that the blower can overcome. A more powerful motor and more efficient air-moving technology enable a blower to overcome more pressure.
The pressure range for low-pressure air can dip below 1 atmosphere with lobe blowers. For screw blowers, which use technology similar to that of screw compressors, the pressure range extends up to 22 PSI. Low-pressure screw compressors, which have applications in deeper WWT systems, can achieve pressure of up to 58 PSI.
Site Conditions
Operating conditions can significantly impact the choice of blower technology. Among the key factors to consider are:
- Temperature
- Ambient pressure
- Indoor or outdoor location
- Seasonal/climate variation
- Available floor space
- Site contaminants (dust, methane, H2S, or other hazardous gases)
Turndown
Oxygen demand is rarely steady state in WWT. For optimal efficiency, a blower must be able to deliver whatever amount of air is required at any given time. Turndown is the ability of the blower to reduce airflow below maximum capacity to match demand, and to increase again as required. Typically, a dissolved O2 (DO) sensor is submerged in the treatment tank, and readings are fed back to a control system in the blower itself or to a centralized plant-level system. Based on the DO readings, the blower adjusts flow to match demand.
According to the U.S. EPA, the fine bubble aeration blower system used in a typical WWT plant can account for up to 70 percent of the facility’s entire energy usage. As a result, matching airflow to demand will drive energy savings. Blowers with variable speed drives (VSDs) can adjust their output to match demand automatically. In systems with multiple blowers, another approach is to simply turn individual blowers on or off as demand varies.
Older technologies with lower capital cost, such as lobe blowers, often lack the energy efficiency of more sophisticated technologies, such as screw blowers. But the additional capital cost of screw machines is returned in lower energy costs, sometimes in a matter of months. What’s more, as WWT tank depths continue to increase as operators seek to expand capacity without expanding their footprint, screw blowers and low-pressure screw compressors can provide both greater O2 transfer and greater energy savings.
Redundancy
Aeration levels in WWT are typically five to seven times higher than would naturally occur. If a system suddenly doesn’t have that higher oxygen level, the bugs will quickly begin to die. WWT systems can take days or weeks to get into balance, so system operators can’t take that risk. As a result, WWT systems typically have multiple blowers to provide a degree of redundancy that enables the process to continue in the event a blower needs maintenance or repair.
Systems are often specified to maximum flow, with a machine in reserve so redundancy is always accounted for. Sometimes blowers are connected to separate energy sources, so if power is lost on one system there may still be power on the other system. Some operators employ a load-balancing strategy using either a controller or manual switching between primary/secondary/redundancy roles. That helps ensure the same number of run hours, maintenance and lifecycle on each blower. A remote monitoring system — such as Atlas Copco’s SMARTLINK system, which employs a cellular connection — keeps system operators informed about blower operating status anywhere, anytime.
Costs
Updating your WWT could feel like a job for another day — something to address when an issue begins to arise. Often, system replacements need to be taken offline individually, in sequence, and utilize backup blowers in order to minimize the risk to the technically sensitive process.
However, by replacing traditional aeration process lobe air blowers with modern variable speed drive rotary screw blowers, a plant can achieve continuous, uninterrupted operation, with a reduced maintenance program saving up to 30 percent of energy costs — plus the potential for further savings by optimizing control systems.
Take Scottish Water’s Nigg wastewater treatment works as an example. The plant’s original 19 blowers of four sizes were reduced to 17 Atlas Copco ZS VSD screw blowers of similar size. This comprised 11 x ZS30 machines and 6 x ZS160 units, all of which feature built-in inverter drives and Atlas Copco Mk5 control and regulation systems to maximize performance under a variety of conditions. The reduction in number of blower units has enabled extra capacity per blower and wide turndown function to match process demands. The ZS machines can run at considerably reduced loads while delivering the same or larger volumes of air as the previous 19 units did before.
As of now, the site is reporting around 25 percent energy savings in aeration, with potential for further savings through DO (dissolved oxygen) control process optimization. This is made possible by the ZS VSD screw blower’s turndown capabilities and superior internal air compression.
Blowers in WWT Other Applications
Other applications for blowers in WWT systems include:
- Filter backwash (common in water treatment)
- Membrane scouring (membranes to encourage bacterial growth, air/bubbles to purge the surface so the membranes don’t get clogged)
- Bio-sparging (employed in the treatment of waste in oil, gas, and chemical plants)
- Process oxidation (industrial processes that require O2 to break down non-biological waste)
Paul Petersen is the municipal sales manager at Atlas Copco. Atlas Copco designs, engineers, manufactures, sells, and services all types of low-pressure air blower technologies. Visit https://www.atlascopco.com/en-us/compressors/locate-us to learn more.