ConAgra Beefs Up Export Packaging with New Trayformer
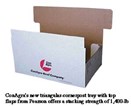
Looking to improve both efficiencies and consistency of quality in its export operations, international food giant ConAgra recently took delivery of a new Pearson model H108 Adjustable Trayformer at its Grand Island, NE, plant for export packaging of vacuum-packed beef products.
"This new box has enhanced the efficiencies in our plant and at the same time shows ConAgra's focus on the needs of our important international customers, says David Peterson, vice president of Export Operations.
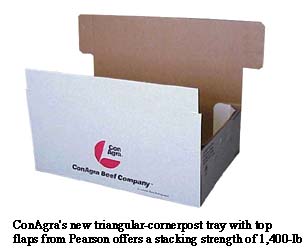
"Our goal is to ensure consistent quality from our door to theirs," Peterson continues. "This new box is designed in a manner to increase stacking strength and at the same time allows us to pack product in a manner that will meet the requirements of our quality-conscience clients."
Triangular-cornerpost Tray
The Pearson model H108 Adjustable Trayformer produces a complete triangular-cornerpost tray (box) with top flaps from a corrugated flat blank at rates up to 18 trays per minute. The triangular-cornerpost construction gives the finished tray a stacking strength of 1,400-lb, producing the box that is able to withstand the rigors of export shipping.
The H108 can be configured to form trays of various styles and dimensions for use in packing meat, poultry and any other heavy product that requires strong packaging and the ability to stack and ship products without damage.
"We think of this box as a miniature display case," notes Peterson. "It is important on how the product fits and how it is protected during transit and storage. Product presentation is very important; the product looks better to the final customer when the box is finally opened."
Automatic Operation On-demand
The machine forms and seals laminated triangular-cornerpost meat trays that have partial overlap (POL) top flaps. The trayformer hopper holds flat corrugated blanks that are fed by vacuum pull-down. Flights transfer the blanks through a special folding and sealing section where laminated panels and triangular corner posts are formed.
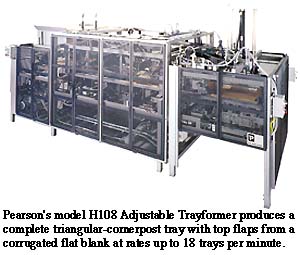
Another set of flights engage the hand holes in the tray and provide alignment to laminated flaps during sealing. The tray continues into the forming section, where a pneumatic-powered mandrel presses the blank downward through flex-mounted plows that fold the end and sidewalls up, leaving the tray to set in a compression chamber to firmly seal the corners.
The completed tray with its top flaps open and erect is released to drop onto the user's conveyor beneath the model H108 as the next tray is advanced into the forming station. Operation is automatic and on-demand.
"Customers also appreciate the benefit of our ability to fill orders quickly and accurately with this box," adds Peterson.
Multiple Features
Features of the new Pearson model H108 Adjustable Trayformer include a vertical hopper with 24-in (610-mm) capacity, a Gast 3040 vacuum system, a main drive with a 1.5-hp motor, a heavy-duty gear box and overload clutch, and a two-stage flight system. Dual Nordson 3700 glue units with temperature setback feature digital display, reduced cavity H200 series guns and a 15KVA three-phase transformer.
The system's laminating section is equipped with powered horizontal belts. A powered lift of the laminating section provides easy access for clearing jams. Timing and control is provided via an Astro Systems programmable limit switch.
Handling trays ranging in size from 33 to 43-in L (838-1,092 mm) to 50 to 60-in W (1,270-1,524-mm), the system's heavy-duty tube frame construction (1/4-in sidewall) is modular to facilitate ease of installation. The trayformer offers durable expanded, electrically interlocked metal guards and a "Steel-it" polyurethane enamel finish.
For more information: Jon Donovan, marketing manager, Pearson Packaging Systems, 8120 W. Sunset Hwy., Spokane, WA 99224, Tel: 800-732-7766, Fax: 509-747-8532, Email: info@pearsonpkg.com.
Edited by Bill Noone, Managing Editor, Packaging Network