Why Is Flexibility In Food Metal Detection Important?
By Melissa Lind, contributing writer
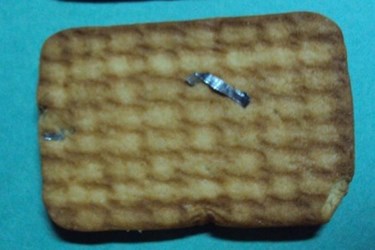
Most metal detection systems have a range of detection capabilities, detecting all types of metal regardless of shape. However, in the highly-competitive food industry, you may demand great performance capabilities from your food product inspection system.
Food safety remains a top issue for both regulatory agencies and the public and food companies are struggling to remain ahead of stringent food safety regulations, such as FSMA. New rules are forcing food manufacturers to shift focus from a perspective of reaction to one of prevention. As part of this process, and with the increasing use of automated processing equipment, food inspection technology, such as metal detection, is becoming an absolute necessity.
While a simple metal detection unit may be sufficient for some food processing lines, the more flexible your system, the better off your business may be. One of the ways that businesses expand is by offering a greater variety of products. To avoid substantial outlay in terms of equipment and space, manufacturers and processors have to multi-purpose their equipment. Production and processing lines can be configured any number of ways.
A particular line may be used for a variety of products, each running singly in different shifts. Others may configure equipment to run multiple products into packaging simultaneously. No matter what the configuration, metal fragments cannot be allowed to enter the food supply.
Adapting To Market Change
It would be great if demand of your food products was steady, requiring that as many number of units your company can produce be produced every day. In the food industry, that just isn’t so. Consumer tastes change, demand is seasonal, and production changes are required. It is vital that manufacturers can respond quickly to changes in the market. Newer metal detection systems are able to cover a variety of product configurations, processing speeds, and packaging types. Making use of advanced technology that includes multiple detection frequencies and sophisticated algorithms, every type of metal in just about every fragment shape can be detected in challenging applications.
These systems are able to handle difficult packaging types, such as plasticized metal and tricky products, such as wet and/or warm food products. Both of these were previously prohibitive. Flexibility within the processing line also allows for multiple product types to run on the same equipment. Production speed can vary and some units allow for the inspection of different products at the same time. This gives manufacturers the capability to vary production capacity, quickly changing a production line, increasing speed, or running more than one line simultaneously. This ultimately gives the packager or processor a business advantage in quick response to changing demands.