Using Scientific Methodology To Ensure Good Weighing Practices
By Melissa Lind, contributing writer
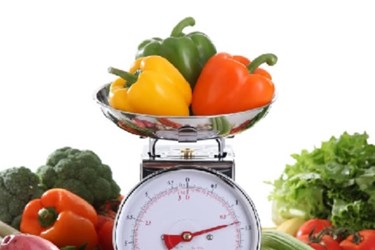
Most food processing lines have some sort of system for ensuring weight uniformity, whether in-process or at the finish point. While this may be adequate most of the time, failure to ensure accuracy can contribute to a higher than desired out-of-specification measurement rate. Implementing scientific methodologies for check weighing can cut down on rejects and improve the bottom line
Out Of Specification (OOS) results have an impact on not only quality and safety, but also production time and efficiency. Too many OOS results can result in costly delays, recalls, and investigations. This has always been true, but in light of new and more stringent regulations due to technology development and global food sourcing and supply, food manufacturers can expect that additional requirements for food-safety standards and inspection processes may be on the horizon.
Podcast: Best QA Practices In Metal Contamination Control
There are many different systems that can be used to assess weight, but some are installed and forgotten with the assumption they are functioning as expected. In addition, existing instruments may have been modified to be used for a different purpose than what they were intended to do, making accurate calibration and adjustment difficult.
Most food regulations call for “periodic” calibration and adjustment on weighing equipment, but levels of accuracy or methods of verification are not generally specified. Consequently, there is a wide range of procedures being used throughout the industry, and often scales are the last place considered suspect when an OOS result occurs. Using a scientific method to set weight standards will help ensure accuracy and preserve efficiency in the food processing line. It will also help to identify causes of OOS results and identify where adjustments are needed.
Measurement Uncertainty And Minimum Weight
Measurement uncertainty is a factor of the instrument’s capability. If an instrument is capable of measurement in a certain range, then the closer you get to either end of the range —large or small — the less accurate the measurement will be. An example in everyday terms would be the lack of ability to measure the weight of an infant on a scale intended for adults.
White Paper: Choosing Between Weight & Mass Inspection — Making An Informed Decision
The minimum weight needs to be defined by calibration with comparison against known standards. You need to ensure that you are operating within the defined accuracy range with a safety margin of at least two so that the minimum amount actually weighed in practice is twice the minimum weight defined by the calibration. In addition, instrumentation capabilities, change over time, and the system should be routinely checked to ensure that the accuracy range remains the same.
Routine Testing
Verification of the accuracy of actual production measurements should be performed on a regular basis. Regulations are vague on these procedures and methods for testing will need to be determined at the plant level, based on the specific technology. Once determined, they should be followed as part of a set procedure.
Using “Smart Calibration” To Ensure Accurate Weighing
In situ calibration should be initially conducted by qualified personnel to determine minimum weight and measurement uncertainty under normal operating conditions in a “validation” process. Calibration should be done after the instrument is installed with normal functional testing that is determined by the equipment. Repeat testing at established intervals should follow the same procedure as the initial validation with additional tests performed if any adjustments are made.
Testing Frequencies
Regulations are also generally vague regarding frequency, only stating that testing should be done on a routine basis. The frequency of routine testing will be based on required accuracy and the impact of OOS results. More essential weigh points will need more frequent testing, such as vital ingredients in baking processes. Points that have a greater impact on the consumer or business should also be tested frequently. Essentially, the greater impact on the final product, the more frequent the testing should be.
Pneumatic Conveying & High-Accuracy Batch Weighing For The Bakery Industry
Testing schedules should be established as a procedure for the plant and should consider environmental condition changes and operator variability by conducting testing when environmental changes occur and during operation by different operators.