Stiff Competition Endangers Food Safety Diagnostic Companies
By Laurel Maloy, contributing writer, Food Online
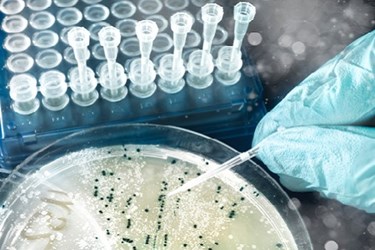
The demand for ever-increasing, competitively-priced, pathogenic food testing is exhausting the limits of some food safety diagnostic companies
The spotlight is shining on food safety brighter than ever. However, the rapidly changing landscape of food testing is proving to be an insurmountable challenge for some pathogen test manufacturers. A number of foodborne-illness outbreaks have spurred the changes that may see the fall of those diagnostic companies that have not kept pace, diversified, or upgraded procedures.
Datasheet: GeneDisc Technology — Food Pathogen Detection
One of the largest and most notorious occurrences is the 2008 Peanut Butter Salmonella outbreak. Sickening more than 700 people in 46 states; nine people lost their lives. Jury selection began in this precedent-setting trial Monday, July 28, and continues today. This highly-publicized case impacted the American population by almost emptying the grocery shelves of peanut butter, a family staple, for months. That meant every time an American went grocery shopping, the empty peanut butter shelves were a source of anger. The empty shelves were a constant reminder of the loss of life and the danger of foodborne illnesses.
Five of the top 10 foodborne illness outbreaks have been in the last 14 years, with one of the most impactful occurring in 1993. An E. coli outbreak traced back to a large, fast food chain restaurant, Jack in the Box, killed four children and infected more than 600 others. The litany of Listeria, Salmonella, and E. coli outbreaks has galvanized the populace, therefore the industry, ensuring the ”old way” of pathogen testing is no longer acceptable. The outcry for in-the-field or on-site testing, and much quicker findings, is causing some pathogen-testing companies to rethink how they do business. Faced with stricter standards and increasingly-competitive pricing, some may be forced to close their doors.
Tips For Complying With New Food Safety Regulations
In the past 15 years, the growth of the global food supply chain, the logistical challenges, and the increase in imports has resulted in a 128 percent increase in overall pathogen testing. The race is on to do things faster and better, for less money. Price per test has become the catch phrase for competition, with the profitability of many diagnostic testing companies taking a huge hit. The move is on to utilizing larger food contract labs (FCLs) and food plant labs (FPLs), leaving independent pathogen test manufacturers scrambling for a piece of the market. The competition is brutal, while all reach to achieve the goals required — accurate, quick, and cost-efficient results.
For example, one of the largest FCLs has been making its own reagents for the past 10 years. This simple step alone results in a savings of $3 to $6 per microbiological test. There is no denying that the prospect of this kind of savings is persuasive. However, the approval of the Association of Analytical Communities (AOAC) is required in the U.S. and there are other regulatory requirements across the world. IEH Laboratories, the FCL referred to above, has already received AOAC approval, with many of the larger FCLs and FPLs expected to follow suit. This, also, could spell disaster for many pathogen-diagnostic companies. Some are already developing automated analysis and sample prep systems, targeting the need for ever more testing. Some are catering to the small and medium-sized FPLs, developing more personalized approaches for pathogen testing. However, there are a large percentage that won’t be able to compete and may be forced out of the food safety testing market altogether.