Reducing The Risk Of Metal-Fragment Contamination
By Melissa Lind, contributing writer
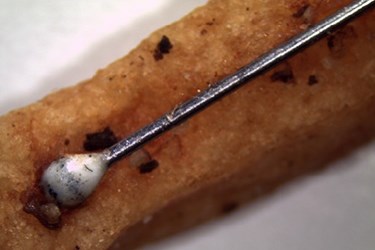
Metal contaminants come in all shapes and sizes, but not all are equally detectable. No matter the foreign-body detection technology employed by your facility, irregularly-shaped metal is the culprit of most food-product recalls.
Because of the increasing use of automation in the food industry, there is an upsurge in metal-fragment contamination. No matter where contamination comes from, food lines running at high speeds can make it difficult for detection systems to keep up. Additionally, conventional foreign-body detection systems may have difficulty identifying irregularly shaped metal contaminants, particularly at small sizes. Wire, shavings, slivers, and filings are caused by broken or improperly aligned processing machinery and most-often enter production lines in the raw or bulk ingredient stage.
Line testing with metal inserted at various points is a necessity and many facilities employ pre-manufactured testing samples, most often are metal beads. Unfortunately, metal contaminants that are spherically shaped are easiest for most systems to detect. The regular surface provides an easy differentiation from other materials and it may be easy to have confidence in a system with limitations. For instance, wires may be detectable when passing through detection systems in a perpendicular configuration, where the system only sees the end profile of the wire, shaped similarly to a bead. This is known as orientation effect and leaves most other wire configurations difficult to detect. Other types of metal contaminants may be too irregularly shaped or too small for equipment to detect at various points.
In addition, adequate testing of metal-detection systems should include varying configurations of known contaminants placed in food products. This process is normally employed with beads, but should also be conducted with all metal types and with irregularly shaped metal fragments at varying sizes close to the limits of the machinery. Utilizing results of Hazard Analysis and Critical Control Point (HACCP) audits will help identify the “where” and “what” regarding the greatest threats. Detections systems should be tested at its maximum stress. This means maximum speeds, more than one product line, and using small, hard-to-detect contaminants.
Using more than one detection unit with varying physical placement so that the food product is scanned from different directions is advised. Choosing to employ multiple detection systems is also an option. Having more units for detecting metallic foreign bodies equates to greater certainty that contaminants will be detected. However, using multiple systems or duplication of current systems at high-stress functioning may seem like overkill. It certainly has a higher cost. What you must ask yourself is, “Can my company afford to have a contaminated product leave the facility?”
The actual cost of recall can be much higher than any capital expenditure in detection systems. It is important to consider actual losses, in terms of lost product, cost of storage, and returns. Then, the theoretical cost may be higher due to increased regulatory attention and for-cause inspections. Finally, the long-term cost is even higher with loss of customer confidence and of brand loyalty. By investing in detecting technology, testing it regularly and vigorously, and following both manufacturer instructions and guidelines created through HACCP audits, metal-contamination events can be reduced, if not avoided.