Quality: Why Meeting Specifications Isn't Good Enough
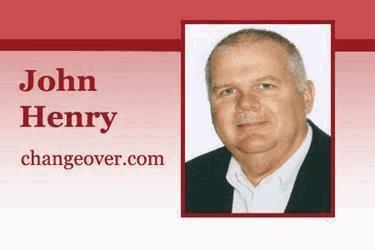
The definition of quality in manufacturing usually contains phrases such as "meeting specifications," "within limits," "fit for use," or something similar. What that definition really says is "good enough," though we seldom hear it expressed that candidly. As long as the parameter is between the upper and lower limit goal posts, it is considered a quality product. In terms of packaging, specifically capping, a nominal 38mm diameter cap that is between 38.2mm or no less than 37.8mm (+/-2mm) is good enough to use.
About 15 years ago, one of my Operations Management students gave me a book that completely changed my thinking. The book was Safer than a Known Way by the Australian Industrial Engineer John S. McConnell.
McConnell agrees that parameters must be within limits, but says it can't stop there. He defines quality as the absence of variation. He does not question that all manufacturing process vary and that we must control them within acceptable limits. His key point is that any deviation from the target is a degradation of quality.
Figure One: Traditional, within limits, view of quality Figure Two: Absence of Variation
This brings a couple of forces to bear on improving the process:
- There is a tendency, conscious or subconscious, to think that as long as we are within limits there is little need to improve. The idea that any variation is a degradation forces us to continuously strive to reduce that variation.
- If the cap diameter varies randomly from low to high limit and back again (Figure One), the mechanics are going to go nuts trying to keep a consistent torque at the capper machine. Even if the machine is capable, it won't do it because of cap variation. If variation is greatly reduced (Figure Two) the cap diameter does not need to be precisely on target. The mechanic can adjust to compensate. Since the cap size is stable, the cap torque will be stable as well.
- Finally, the definition helps show the path to improvement. The random variation shown in Figure One makes it hard to bring the process to the target value since each instance must be corrected individually. When the cap size is stable, it is much easier to move the entire group toward the center value.
It is bad enough when the cap diameter is the only variable, but in this case, there are at least two — the cap and the bottle to which it is applied. Ideally, the bottle must be slightly smaller than the cap, let’s say 37mm. It too has a tolerance of +/-2mm. When a large, but within specification, cap is applied to a small, but within specification, bottle, the threads may not engage properly. When the situation is reversed and a small cap is applied to a large bottle, it may not go on at all.
By John Henry
The Japanese statistician and engineer Genichi Taguchi also did considerable work in this area and developed the Taguchi Loss Function (TLF), which has been incorporated explicitly or implicitly in many quality programs.
TLF, in Figure Three, says that for any variation from the target, there is a quality cost and the further away from the target, the greater the cost. When close to the target value, it may be hard to justify the expense of eliminating the small loss. As we move away from the target value, the cost of the loss increases eventually becoming unacceptable.
![]()
Figure Three
No discussion of quality would be complete without mention of measurement. Variation must be measured accurately and precisely if it is to be controlled. One rule of thumb I have heard is that measurement must be an order of magnitude greater than the target to be controlled. If a dimension is to be +/-0.01," it must be measured to +/-0.001." An excellent discussion of this concept appears as a chapter in Henry Ford's book Moving Forward.
Quality can never be "good enough." We may have to accept something less than perfect, but that doesn't mean we have to like it. More importantly, we must always be striving toward shrinking the limits as much as we possibly can.
About The Author
John Henry has worked in packaging since 1976 and is known as the go-to guy for information on packaging machinery. He is the author of the “Packaging Machinery Handbook” and “Secrets of Buying Packaging Machinery” and has authored more than 60 related articles in the trade press. At his consultancy, www.changeover.com, Henry focuses on helping manufacturers reduce downtime and improve operating efficiency. Got a question, comment, or column idea? He can be reached at johnhenry@changeover.com