Making Food Safety Advocates Out Of Operations Leaders

By Sam Lewis
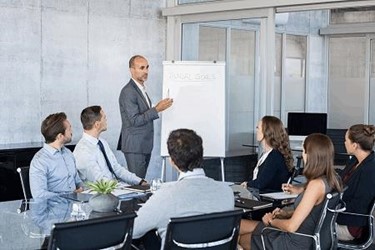
Food safety professionals and food operations leaders share the same goals, but rarely speak the same language to achieve them. Because of this, sometimes processes are not nearly as streamlined as they could be. Here, Charlean Gmunder, a food manufacturing senior ops leader, answers my questions about turning your company’s operations leaders into food safety advocates.
Food Online: What can food safety leaders do to stress the importance of food safety to operations leaders?
Gmunder: There are several ways food safety leaders can work to create a food safety advocate in their operations leaders. I use this simple equation for success: knowledge + shared values + aligned goals = food safety advocate.
By providing knowledge about food safety — the regulations and guidelines — to the operations leader, the food safety professional shares their expertise with their associate. This helps the operations leader to better understand the decisions that must be made regarding the process and the product. In addition, by understanding what drives an operations leader — their characteristics and responsibilities — the food safety professional gains a knowledge of the motivational factors that are useful in creating shared values.
It is important for the food safety professional to get the operations leader to understand how achieving the food safety goals will directly and positively impact their own operational goals. That clear correlation of goals, along with the basic knowledge of food safety, using an approach that recognizes the operations leader’s attributes, will bring success in developing a food safety advocate.
The operations leader will not just provide support to the food safety professional, the operations leader will be a true representative of food safety within the organization. This is what we must achieve to operate successfully in today’s food industry.
Food Online: Expand on the aspect of knowledge… what kind of knowledge is needed — food regulations, HACCP, Global Food Safety Initiative (GFSI), customer demands? How can food safety leaders educate operations leaders?
Gmunder: I recommend a multifaceted approach to educating the operations leader about food safety. Many food safety professionals assume the operations leader understands the regulations under which they operate. You should never assume this, regardless of the number of years the operations leader has worked in the food industry. It is important for the food safety professional to share their expertise by providing the operations leader with knowledge of the specific governmental regulations — FDA or USDA — relevant to their segment of the industry. It is also critical that the operations leader knows what are the practices and procedures their company uses to meet, or exceed, those regulations. In addition, the operations leader needs to be knowledgeable about the GFSI scheme that the company uses and understand the guidelines — as well as the processes and procedures the company has chosen to use to comply with those guidelines.
To truly get the operations leader engaged in the learning process I believe the food safety professional needs to take the ops leader into the plant during the sanitation process and have the operations leader observe all the steps of the process, including pre-op. Additionally, the food safety leader should ensure the ops leader understands the swabbing techniques and the results being found.
It’s also important to have the operations leader participate in management reviews. It would be ideal if the operations leader was a participant in the internal audit process, but this may not always be feasible. At the very least, the operations leader needs to understand what the findings of those audits are and what actions are being taken as a result. In reality, it’s the ops leader’s facility and, ultimately, the ops leader’s responsibility! He/she needs to know how the facility is performing.
Food Online: Explain shared values. How can food safety objectives help achieve operations’ goals? What can a food safety leader do to reinforce the importance of avoiding negative incidents and occurrences, such as lost revenue and profits, decline in market share, and legalities?
Gmunder: One important aspect of educating the operations leader that should never be overlooked is the need to ensure the operations leader knows what the implications of failures to the food safety system are. By this, I mean the food safety professional should share examples of companies that have had failures and show what transpired as a result. Nothing hits home as clearly as an example with a competitor or someone from a similar segment of the food industry. When the operations leader realizes how the failure impacted the profitability or the market share, it can really be impactful.
If that doesn’t get the leader’s attention, showing what happened to people in a leadership position, from the legal perspective, certainly should do the trick! No one wants to use scare tactics to ensure compliance, but it’s important for the operations leader to truly understand that these situations are reality; they can, and do, happen, and the negative implications can be substantial. The food safety professional cannot assume that the operations leader is as aware of these situations as they are. This is a very necessary part of the process of educating the operations leader.
Food Online: How can operations leaders be influenced to understand that achieving safety objectives will help them achieve their operations goals?
Gmunder: Operations leaders are responsible for a great number of things, but one thing they must be cognizant of is how food safety objectives are directly related to their goals. There’s no better person to show them this than the food safety professional.
In order to do this, I recommend the food safety professional understand two things: First, the typical traits of an operations leader and then the responsibilities of the operations leader. In order to do this, the food safety professional needs to be open to Stephen Covey’s wisdom, “seek first to understand, then to be understood.”
While not all operations leaders are the same, most share very similar characteristics. As a rule, operations leaders are achievement-oriented; they like to get results. They are also data-driven. This means that they are looking for the analytical information before making a decision. Many operations leaders are focused on outcomes and timelines. They look for detailed plans. And, oftentimes, they are interested in creating sustained improvements, meaning they are process-oriented. Because they encounter issues in their day-to-day duties, they also tend to be good at problem-solving. And, because they are generally responsible for large teams of people, they have to be good communicators. So, for example, if we know the operations leader tends to be focused on outcomes and timelines, it would be best to approach him/her with a clearly-defined plan that outlines milestones and expected results.
Another important aspect for the food safety professional to be aware of is the responsibilities of the ops leader. Regardless of the size of the organization, all ops leaders are generally responsible for four key things: safety, food safety/quality, cost, and service. The operations leader is held accountable to ensure that all associates at the facility work in safe conditions, in a proper manner, using the appropriate equipment. They also are responsible for producing product that meets the required quality and food safety guidelines, and at the targeted costs. In addition, they must provide an acceptable level of service for customers.
By recognizing the responsibilities of the operations leader, it becomes easier for the food safety professional to direct goal alignment by demonstrating how achievement of a food safety objective supports those things that the operations leader is concerned about. This level of understanding helps the food safety professional to tailor their approach to the operations leader and to ensure it hits home with the leader’s focus.
Food Online: How will you know when sufficient trust and cooperation have been established with operations leaders so a successful food safety program can be implemented and sustained?
Gmunder: A food safety professional will know a true collaborative environment has been established when issues are brought up by members of the operations team. This will be seen when members of the operations team are pushing for improvements as a result of internal audit findings or, pre-op findings, as well as from customer complaint data.
When the QA/Food Safety team is no longer the ones pushing — when they find their operations coworkers driving for improvement alongside them — it will be obvious to the food safety professional that they have established a food safety advocate in their operations leader, and he/she has led the organization to a sustained food safety culture.