How Can X-Ray Detection Systems Save Your Company Money?
By Melissa Lind, contributing writer
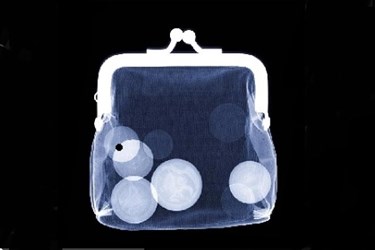
Installation and implementation of an X-Ray system to detect foreign bodies in your food-processing line may have a hefty price tag. However, if you consider the consequences of product recalls, forced inspections, and lost customer confidence; the cost of investment is actually a long-term money-saver
Even though the up-front cost may be considerable, new advances in the abilities of X-Ray technology can dramatically improve your company’s bottom line in the long run. Still skeptical of X-Ray inspection systems’ benefits in light of continuing news of product contamination and increasing food-quality and safety guidelines? Do your own analysis. Consider how much you spend on product recalls, batch rejection, or line stoppage due to contamination issue. Then consider these additional points in favor of X-ray inspection.
Reduced Labor Costs
After installation of an automated X-ray inspection system, immediate cost-savings in terms of workforce hours can be seen. Automated X-ray technology — unlike older, foreign-body detection systems — does not require hands-on, or even eyes-on, supervision. Though other cost savings attained through installation of new technology may take some time to see, worker time can be freed up immediately.
Allocate Resources More Efficiently
When you have saved workforce hours by implementing an automated X-Ray system, those work hours gained become critical to other areas of your company’s production. Instead of using those workers in menial, repetitive tasks, you can approach improvement in other areas of your facility. This may allow you to expand production either in quantity or by introducing new products or new methods to boost revenue.
Pinpoint The Problems
Depending on your particular processing line, X-Ray detection systems can be placed at any critical point. Pinpointing the most-likely source of contamination can save the whole batch, but just rejecting a few portions.
Case Study — X-Ray Product Inspection Takes On New Food-Safety Regulations
X-Ray detection systems can be flexible with multiple detection variability. Not only do they detect foreign bodies, such as metal or hard contaminants, they can also check for:
- Product weight, within specifications
- Individual product count
- Packaging irregularities — broken caps, improper seals, missing packaging elements
- Product consistency — conglomerations, lumps, inadequate mixing
- Product positioning
X-Ray detection systems can be used at virtually every point in the food processing line, whether needed for ingredient examination or final-product check, and placement can be based on your specific product.
Protect The Product Image
Ensuring that contaminated products do not ever reach your customers enhances your company’s bottom line by protecting your product image and ensuring brand loyalty. Just one mishap in contamination can dramatically affect the way your customers feel about your product. While your advertising and customer engagement is important, brand identity and company identity is mainly established by the product itself. Poor quality control can tarnish your company image and more so if the product has to be recalled.
Avoid The Inspection Headache
Compliance with standards in food product quality, including HACCP standards and the Global Food Safety Initiative (GFSI), through the use of X-ray technology can prevent not only costly recalls but also facility stopping events such as for-cause inspections which cause work stoppage and product delivery delays.