Heinz And Ford Turn Tomato Skins To Automotive Parts
By Karla Paris
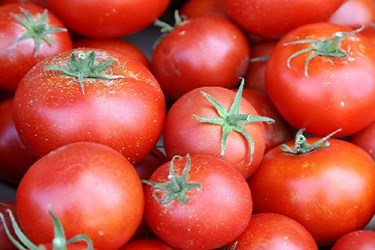
Partnership could give the ketchup maker a sustainable and profitable outlet to dispose of its processing waste
Imagine rolling down the road in your car after you have just replaced your old tires with a new set made from old tomato skins.
What?
Well, it might not be tires, but if Ford and Heinz’s research is on target, the Pittsburgh-based ketchup maker and the Dearborn, MI-based motor company could be turning tomato skins into auto parts.
According to a joint news release, scientists at both companies believe they can use tomato fibers to manufacture composite materials used for wiring brackets or storage bins in cars instead of petroleum-based plastics. The venture would be a big win for both companies, especially Heinz, whose researchers were looking for innovative ways to recycle and repurpose peels, stems, and seeds from the more than two million tons of tomatoes the company uses annually to produce its leading product, ketchup.
Nearly two years ago, Ford began collaboration with Heinz, Coca-Cola, Nike, and Procter & Gamble, among others, to accelerate development of a 100 percent plant-based plastic. The group believes this material could be used to make everything from fabric to packaging with a lower environmental impact than petroleum-based packaging materials currently in use. To date, the group has used everything from retired U.S. currency and blue jeans to wheat, straw, and mushrooms to manufacture more environmentally-friendly car parts, such as storage bins.
Case Study: Heinz Frozen Food Boosts Efficiency With Infor EAM
During a phone interview with Inhabitat.com, a weblog devoted to the future of design, bio-plastics expert and lead researcher Dr. Ellen Lee explained that the byproduct of Heinz sauce production would be mixed with polypropylene and cooked at a lower than normal temperature so that the natural fibers are not degraded. This not only means less energy is required to manufacture the bio-plastic — which will be comprised of 20 percent tomato fiber by weight— but because the tomato waste replaces talc material currently used, the bio-plastic is also lighter.
At Heinz, every stage of its operations presents an opportunity to eliminate waste. For example, its factory in Jacksonville, FL implemented a recycling project that has diverted approximately 50 percent of its solid waste to recycling, the equivalent of 3.7 million pounds per year or 185 trips with the average garbage truck. Concepts, such as this partnership with Ford, have allowed the company to reduce, reuse, or recycle to divert solid waste from landfills.
Heinz has sought beneficial uses for all waste globally through its sustainability process, which taps a comprehensive network of regional sustainability coordinators who share best practices in resource management and recycling with its facilities. Since 2005, Heinz has reduced waste by nearly 52 percent per 100 metric tons of production globally.