Follow These Steps For A More Energy-Efficient Cold Chain Facility (Part One Of Two)

By Sam Lewis
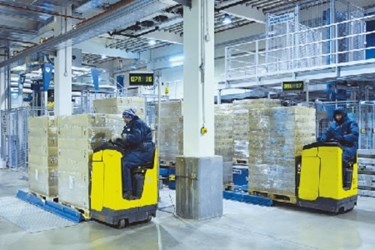
An uninterrupted, temperature-controlled supply chain is the key to keeping fresh foods from spoiling. However, this practice often comes with a hefty initial investment and increased energy costs. Here are seven points to help your company’s cold chain reduce its footprint and help the bottom line.
A report titled, “Global Frozen Food Market Analysis by Products Type and by Geography — Trends and Forecasts (2010-2015),” the frozen food market will have grown by more than $40 billion between 2010 and 2015. Obviously, this is a lot of money. Cold chain logistics is an expensive practice, but investing in it is an intelligent business move. In a well-functioning cold chain, the shelf-life of many fresh products can easily be doubled. This extended shelf life increases return on investment (ROI). In an already-expensive market that is only expected to continually grow, increasing ROI is a smart move.
What’s The Impact Of Big Data In The Cold Chain?
VSLs, Cleanliness, And Temperature Control
Loading docks should be temperature controlled and supplied with specialized equipment to do so. Included in this equipment are vertical storing dock levelers (VSL). These store upright and inside the facility, offering excellent energy efficiency. A clean, energy-efficient environment is important for fresh food. The ability to clean in, around, and below a dock leveler is a huge benefit and VSLs provide this during washdowns. Finally, VSLs allow dock doors to be sealed tightly. No gaps and eliminated spaces between floors and doors minimize chances of energy escaping, ultimately boosting efficiency.
Hydraulic Rail Levelers
Multi-function distribution modes are being taken on by many facilities due to increased customer satisfaction and faster ship times. This is especially true in cold chain operations. A company may have one division handling all aspects of its fully-functional refrigerated services — warehousing, inventory, and distribution — for perishable goods. In many of these cases, train deliveries are received directly to facilities. This is a hydraulic rail lever (HRL) is the best solution. HLRs share the same standards of safety and power as VSLs, while having the ability to unload deliveries from the railcar straight to the storage facility. This, in turn, provides easing sorting, storing, and distribution for all other parties.
Ensure Efficient Dock Seals
Ensuring a climate-controlled facility remains energy efficient is an enormous task. With what seems to be an infinite amount of opportunities for energy to be lost, the challenge of optimizing energy use can be overwhelming. But a few, initial moves can save many headaches down the road. Dock seals and shelters can be interconnected with equipment in the loading dock—doors, vehicle restraints, and dock levelers — ensuring the right sequence of operation and boosted energy efficiency. Dock seals are just as important for cold storage as the levelers, doors, and other essential equipment.
Assessing your facility is important. Do I need full access to trailers during loading and unloading? Do swing door trailers frequent the loading dock? These questions are important to ask yourself because while seals are the best solution to saving energy, some seals hinder access to the entire trailer. This makes it difficult for loading and unloading. Additionally, seals that overlap into the trailer are often torn during loading/unloading cycles. A ripped seal is as efficient as no seal.
Why Monitoring Cold Chain Data Is Not Enough
Prevent Energy Loss
Dock seals and dock shelters are both efficient means of energy savings. But deciding between them can be a difficult chore. Conventional dock shelters give full access to trailers. However, when trailer doors are opened, many gaps are created. These gaps allow an air exchange between the facility and the trailer. This increases the risk of product spoilage and is not an efficient use of energy.
Dock shelter systems start working as soon as a trailer backs into a dock. The shelter is automatically activated by the trailer as both sides are grasped and hinge gaps are covered. The seal is full, consistent, and unrestricted access to the trailer is given for loading and unloading. This essentially eliminates the risk of spoilage of fresh foods and energy loss.
In part two of Follow These Steps For A More Energy-Efficient Cold Chain Facility, the final three steps of creating an energy-efficient supply chain will be explored. Included in them are: securing trailers and enforcing safety, increased air flow and how it leads to efficiency, and how to tie of the steps together to optimize you company’s cold chain facility. Stay tuned.