Dissolved Air Flotation(DAF) Clarification For Wastewater Pretreatment Reaps Benefits for Bacon Processor
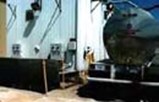
Table of Contents
Wastewater Pretreatment Operation
Flocculation Tubes
Sludge Disposal
Dissolved Air Floatation (DAF) Clarifier Operation
Regulatory compliance management at Marburger Foods Inc. (Peru, IN) report they have taken advantage of dissolved air flotation (DAF) clarification technology in their wastewater pretreatment system for their pre-cooked bacon processing operation. In particular, new capability for salvaging fat has been gained, and continued municipal discharge compliance has been assured for projected wastewater flow increase from plant expansion.
The three DAF clarifiers at the site were manufactured by Precision Environmental Systems of Springfield, MO. Two units for the first stage of pretreatment began operation in mid-1996, and the special unit for second-stage pretreatment, including a flocculation tube assembly, started up in late 1997.
"The results have been excellent," said Jim Walsh, Marburger's regulatory compliance director. "We're probably pulling off fat at an average rate of 35,000 lbs/week, which was more than we anticipated, and the sales of which have already more than paid for the first two DAF units. And since the installation of the third unit in an expansion of the pretreatment operation, we're showing compliance parameters well within the mandates of our state NPDES permit, including oil and grease below detectable levels."
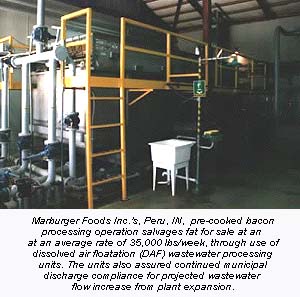
Walsh said the company abandoned its previous lagoon wastewater system in order to gain capability for recovery of fat, which is sold primarily for livestock and pet food. In addition, there was no room for lagoon expansion that would have been required to allow continued regulatory compliance for projected increased wastewater flow.
The company's customized NPDES permit for municipal discharge, developed by the Indiana Department of Environmental Management in consultation with the municipality of Peru, calls for a pH within 6.5-8.5; Total Suspended Solids(TSS) within 250 mg/l; Carbonaceous Biological Oxygen Demand(CBOD) within 200 mg/l; and oil & grease within 100 mg/l.
Walsh reports that their two-stage DAF pretreatment process has typically reduced oil & grease from 140 mg/l to < 4 mg/l; maintained a pH of 7.1-7.6 without any need for adjustment; lowered TSS from 812 mg/l to 48 mg/l; and reduced CBOD from 1760 mg/l to 42.3 mg/l. In addition, dissolved oxygen measurement increased from 0.3 mg/l to 4.7 mg/l., "demonstrating a good level of oxygen in the activated sludge tank". (see Table 1)
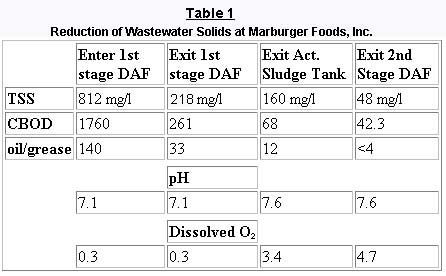
Wastewater Pretreatment Operation
In the first stage of DAF pretreatment, 70,000 gal./day of process wastewater flows from two plants into concrete receiving pits, which serve as temporary flow equalization tanks. The wastewater is then pumped from the pits into two DAF units, where fat is skimmed off and pumped to a tanker. The first-stage DAF effluent drops into twin concrete receiving pits, and is then pumped to a common, 150,000-gal. flow equalization tank.
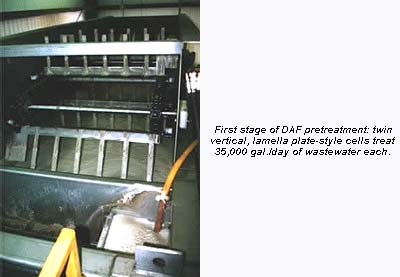
In the second stage of DAF pretreatment, water from the common flow equalization tank is pumped into a third DAF unit, which the manufacturer describes as a unique "split" type. Water enters one side for treatment, and is then discharged to a 250,000-gal activated sludge tank. Discharge from the activated sludge tank feeds back to the other side of the "split" DAF unit for further treatment before being gravity fed to the city sewer. Sludge from both sides of the unit is skimmed off and pumped to a sludge storage tank.
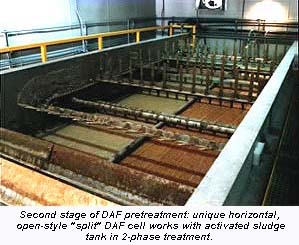
Walsh added that the second-stage, "split" DAF unit was equipped with flocculation tubes for each side.
"Each tube assembly contains multiple ports for injection of polymers, coagulants, and pH monitoring," he noted. "We're running a polymer dose of 2-4 lbs./day on the first side, and 1-2 lbs/day, only when needed, on the second side."
Sludge is disposed via land injection according to the terms of a state land application permit. Farmers receive the sludge as free fertilizer in return for allowing it on their land, realizing an agricultural value of about $40/acre.
Dissolved Air Flotation (DAF) Clarifier Operation
Precision Environmental Systems says the first stage of the DAF pretreatment operation, which began in mid-1996, uses twin vertical, lamella plate-style cells. The company says the second stage, which began in late 1997, features a unique horizontal, open-style split DAF cell. According to a spokesman, the vertical style was chosen because of higher flow rates and lower solids loading, while the horizontal version was specified for lower flow rates and higher solids loadings. Each is said to be constructed entirely of 304 ASME Certified Stainless Steel.
Flocculated wastewater enters each DAF Cell through a Flow Distribution Manifold. As the water passes through the manifold, it is mixed with a side stream of recirculated, clarified water that contains very finely dispersed dissolved air. The dissolved air is produced by a highly efficient, stainless steel, multi-stage pump that maximizes the solubility of air in water.
The dissolved air creates microscopic air bubbles, 30-50 microns, that easily attach to solids particles and carry them to the surface of the water, completing the process of flotation. The floated sludge is then skimmed off and transferred for removal and/or recovery. The clean water, now substantially free of solids, is ready for discharge or further treatment.
Precision Environmental Systems, a division of Precision Stainless, Inc., provides custom designed, engineered, and manufactured DAF Cells and systems for a variety of applications, including meat, poultry, citrus, dairy, fish, and other food processing plants; laundry, cleaning, and mining operations; textile plants; tanneries; refineries; and bakeries. They are designed to remove the majority of all suspended solids, fats, oils, and greases, but will not remove anything dissolved in the water, such as sugars and salts. Flow rates range from 15-700 gpm.
The company says systems can be fully automated with Precision Computerized Process Control, manually operated, or partly automated.
For further information, contact Precision Environmental Systems, 3300 East Pythian, P.O. Box 668, Springfield, MO 65801, Tel. 417/865-2240, Fax 417/865-0906. E-mail: dafinfo3@psitanks.com
Edited by Pam Ahlberg