Determining Which Food Inspection System Fits Your Operation's Needs

By Sam Lewis
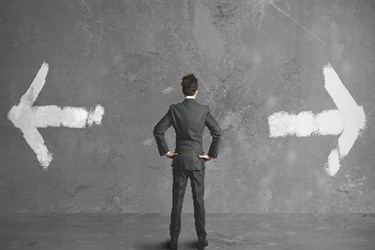
Typically, X-Ray inspection and metal detectors are most-frequently used to detect foreign objects in food production and packaging. But, what things should be considered when deciding to implement a new detection system at your facility?
What Are The Likely Contaminants?
Every division of a food manufacturing or processing facility carries potential to contaminate the end product. However, some contaminants are more likely to occur than others based on what your facility produces. For instance, bone contamination is very possible at a poultry processing facility, but unlikely at a wheat or flour mill. Obviously, bone cannot be detected by a metal detector, so X-Ray would likely be more beneficial to a poultry processor than a flour mill.
Related: Tips For Complying With New Food Safety Regulations
To put it simply, metal-detection systems can identify all types of metal, including aluminum and wires. However, these systems cannot detect other types of solid contaminants — bone, plastic, glass, stone, etc… They are also are not capable of inspecting products by shape, fill level, counting, or weighing. X-Ray inspection systems can detect most metals and an array of other solid contaminants. X-Ray detection can also assist in inspecting products by shape, fill level, count, and sometimes even weight.
What’s The Best Detection Point?
Determining the location in your operation that foreign bodies would most-likely contaminate your product can heavily influence which inspection technology to implement. Metal detectors are versatile in that they can be employed at nearly any point in the production process. However, their performance can be limited by the size of the opening that food products move through. Typically, these systems are best for small-packaged goods and bulk, conveyable products.
Related: Will X-Ray Inspection Replace Metal Detection In Food Processing?
Similar to metal detectors, X-Ray inspection systems are limited by the size of the product passing through the system. However, X-Ray systems have more sensitivity when it comes to larger products compared to metal detection. Because of limitations with scanning rate, X-Ray inspection is under the constraint of speed — it must be constant to create uniform images. This also means that X-Ray inspection systems are not applicable to gravity flow functions. Finally, X-Ray inspection typically occurs at the end of the production line.
Related: X-Ray? Metal Detection? Both?
What Do The Tests Say?
After determining your potential contaminants, their sources, and knowing which point for inspection is best for you facility, you can then begin testing both metal detectors and X-Ray systems for efficiency in your operation. Many factors will influence each application’s performance, so it’s best to test each technology. Your goal should be to make each detection technology fail these tests. The technology you decide upon should provide you with nearly 100 percent detection accuracy, without false readings. Once testing is completed and results have been returned, your facility should have the necessary data to implement a detection system to overcome the trials of your facility.